3 min read
The Future of the TAD Process in the Pulp and Paper Industry
Marcello Collares
:
Jul 26, 2023 12:00:00 AM
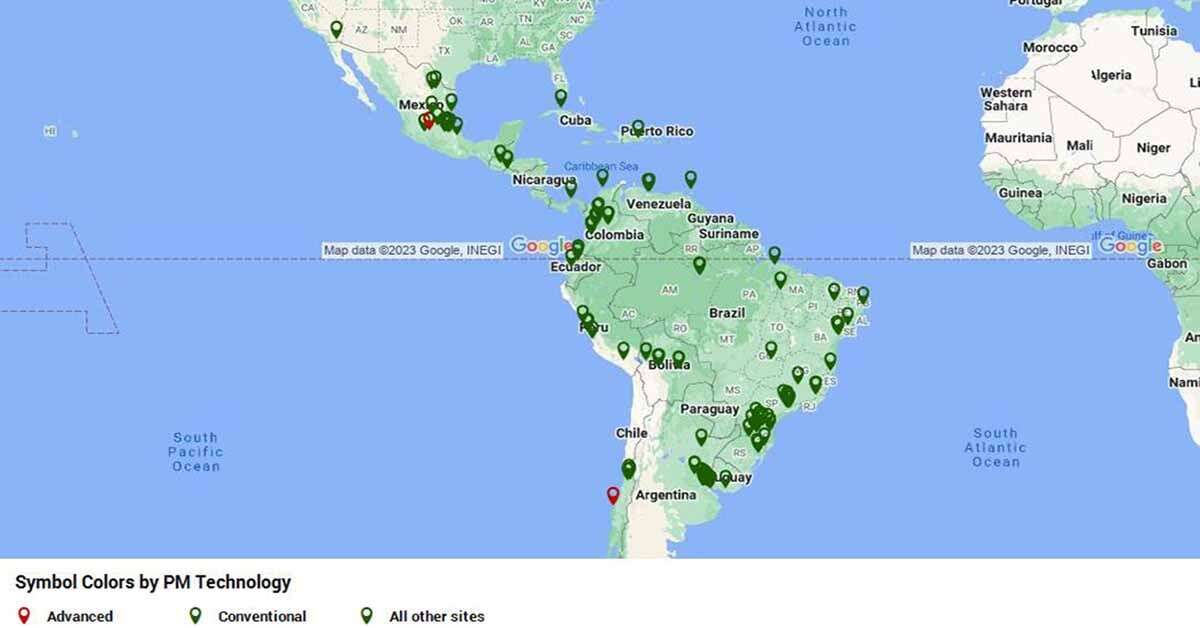
Of all the major pulp and paper grades, tissue and towel is one of the few that directly relates to consumers. While there are others that do the same, none have as much connection as tissue and towel.
Although the tissue and towel sector makes up only 9% of the pulp and paper industry, its market is on an upward trajectory. This presents a wealth of opportunities for producers.
Historically, the tissue and towel sector has remained relatively stable and resilient since its products are essential household items. We saw this sentiment shine through extraordinarily during 2020 when COVID-19 lockdowns were set in place.
Unlike many other sectors, demand for tissue and towel products tends to remain consistent regardless of economic conditions. Although, shifts in consumer preferences and cost considerations can impact the industry.
It also brings interesting and lucrative possibilities for paper producers. Tissue and towel raw materials (cellulose or shavings) are bought in tons while final product sales are made in bales or rolls. The smaller the amount of fiber used to make a bale, the greater the profitability.
Obviously, there are other variables in the search for profitability. But the fiber-by-footage balance is so important that it was one of the reasons for the creation of the Through-Air-Drying (TAD) process and its products.
The TAD Process: What Is It?
The TAD process is used to dry tissue and towel products efficiently while also maintaining softer, bulkier, and more absorbent properties. Conversely, the traditional wet-pressing method is used for conventional papermaking in other sectors.
In the TAD process, the paper web is transferred from the forming section of the paper machine to a specially designed through-air-drying fabric or belt. That belt is permeable, allowing hot air to pass through it and interact with the paper web.
This hot air causes the paper fibers to expand, creating a bulkier and softer product compared to traditional drying methods. After the TAD process is complete, the dried paper web is crêped. This involves scraping it off the drying fabric using a doctor blade. Creping gives the tissue or towel product its final texture, softness and flexibility.
Advantages of TAD
There are several advantages that come with using the TAD process:
- Improved product quality: TAD-dried paper products tend to be softer, bulkier and more absorbent, making them highly desirable to consumers.
- Enhanced machine performance: TAD machines can run at faster speeds and produce higher-quality paper products, leading to increased production efficiency.
- Profitability: Use of the TAD process can help companies generate better prices and margins due to the use of less cellulose.
TAD in Different Regions
The TAD process has gained significant popularity in North America—primarily in Canada and the United States. This is largely due to strong consumer preference for higher-quality tissue and towel products.
In fact, the United Sates has the world’s largest advanced process tissue fleet using TAD or structured technology. 44% of the total capacity is some form of advanced structured tissue.
In Europe, many producers have embraced the TAD process as well. However, the need for higher quality, soft tissue and towel products is not a primary factor. Instead, the goal in using the TAD process is to achieve higher absorbency performance and reduce the total amount of towels required in the market.
Interestingly, there are very few unconventional tissue machines installed in Latin America. This is due to a few factors such as market demand and consumer preference, investment costs, market maturity, and others.
But What About Costs?
The image below depicts a cash cost analysis of tissue production by conventional versus nonconventional machines installed in North America from 2020 onward. When creating this analysis, three key factors were taken into consideration: cellulose, energy and cost of capital.
This analysis shows a cost difference, in the selection indicated, of approximately USD $150/tonne. This backs the sentiment that TAD is now a mature technology than what it once was, so the cost gap compared to traditional machines is much smaller.
This leads us to consider several questions regarding the use of the TAD process.
- What is the added value potential of an unconventional machine and use of TAD in your market?
- What is the value of being a pioneer in investing in unconventional machines in Latin America?
- Is the risk of being a pioneer less than the cost of following the market?
- What disadvantages, such as high energy use, come with the use of the TAD process? Do these disadvantages outweigh the advantages?
ResourceWise’s unparalleled solutions for suppliers, producers and investors in the pulp and paper industry makes answering these questions a bit easier. With our innovative data platform FisherSolve and expert consulting services, we empower businesses to harness their full potential by providing you with real-time insights that drive smarter decisions.
For more insight into how ResourceWise can help you foster business growth, contact us today.