3 min read
What’s Driving the Disparity Between Log and Lumber Prices?
Pete Stewart
:
Mar 31, 2022 12:00:00 AM
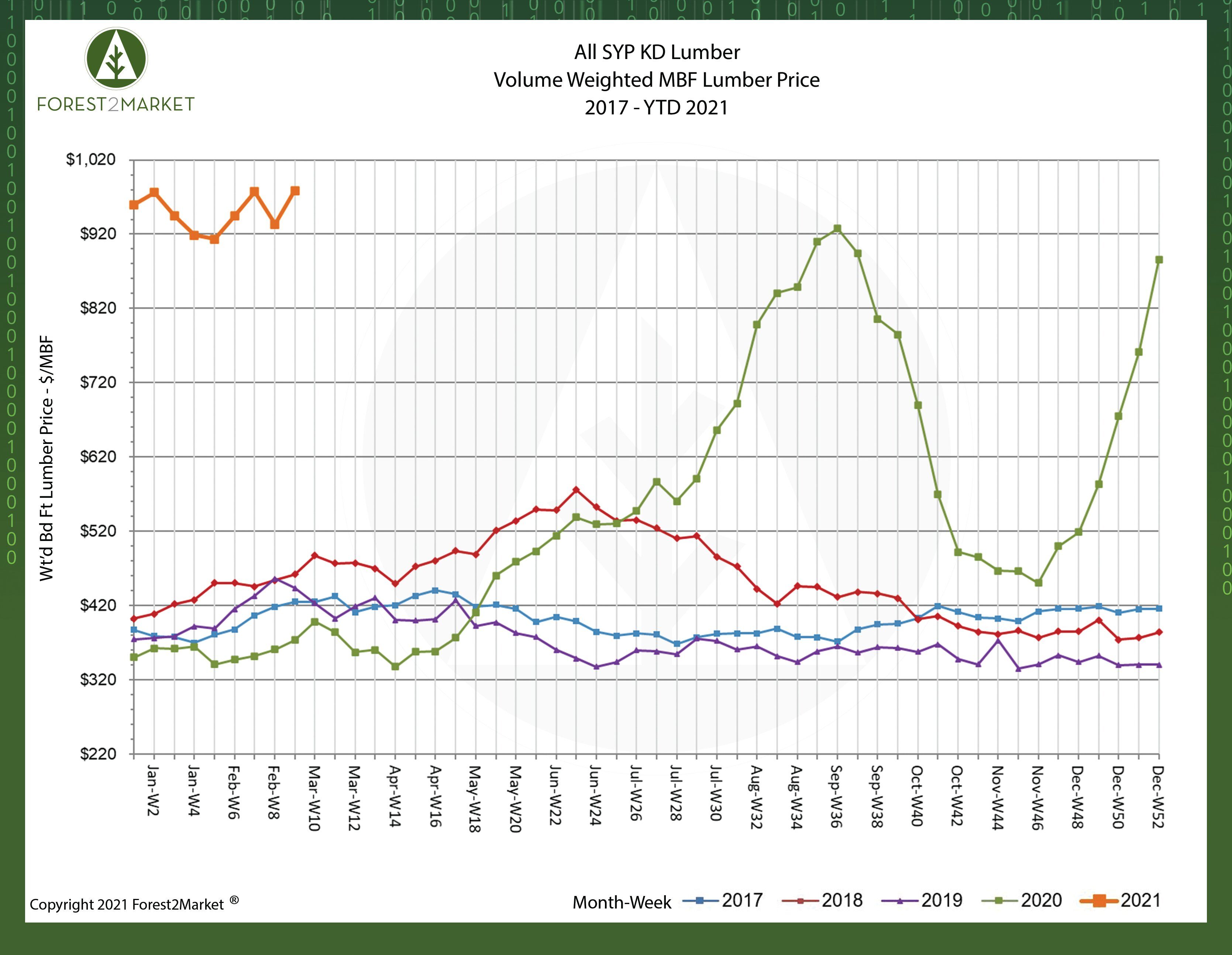
Southern yellow pine (SYP) lumber prices are at record highs, by huge margins. Forest2Market’s composite SYP lumber price for the week ending March 5 was $979/MBF, which represents an astounding 171% increase over the same week in 2020.
While this trend benefits southern sawmills, many timberland owners in the US South are asking the obvious question: Why are log prices in local markets not reflective of a record lumber market?
The answer to this question is not as straightforward as it may seem. While log prices are to some degree tied to lumber prices, the association is a loose one. There are a number of mutual factors that affect both lumber and log prices, but each market also has independent drivers that do not overlap, which is why we see such a stark disconnect between the two markets.
What Market Forces Drive Lumber Prices?
The two primary factors that drive lumber prices are housing starts and lumber inventory.
- Housing starts: Historically, the main driver of SYP lumber prices has been the larger US housing and remodeling markets, which require a well-oiled supply chain, steady import flows (primarily from Canada) and massive amounts of finished lumber, plywood, oriented strand board (OSB) and other building materials.
- Lumber inventory: The market’s capacity to produce lumber is the other key factor that drives price. Manufacturers must be able to make and stock a variety of products in order to meet the demands of the huge construction market.
What Market Forces Drive Log Prices?
The two primary factors that drive log prices at both the mill gate and in the forest are the general economic principles of supply and demand.
- Supply of logs (as standing timber): The inventory of standing timber products in a given supply basin must be matched to regional demand for those products. I.e., pulp and paper mills need access to deep inventories of pulpwood, and sawmills need access to sawtimber. In the US South, over 12 billion tons of inventory are currently growing in southern forests; roughly 280 million tons (3%) are harvested and used in the production of wood products each year.
- Demand from mills: Wood products mills require a significant amount of raw material to manufacture their end products. The cost for these materials makes up a vast majority of a mill’s operating costs—up to 75% in some instances. Of the total annual harvest in the South, approximately 145 million tons of wood go to pulp and paper mills as pulpwood; approximately 120 million tons go into dimensional lumber and panel/plywood production as sawtimber; and less than 15 million tons go into the production of wood pellets.
As I wrote in the immediate aftermath of the first wave of lockdowns in June, lumber prices shot up so quickly based on three primary factors:
- Stronger than expected housing starts and unforeseen demand from the remodel sector
- Capacity and supply chain adjustments
- Market speculation driving uncertainty
Prices then temporarily plummeted in early fall before bouncing back in November, and they have climbed ever higher thanks to a late season rally led by builder-friendly autumn weather. Demand for single-family housing has increased so rapidly in recent months—fueled by low interest rates and a desire for more space—that there is now a gap between sales and home construction not seen since the housing bust that began in 2007. Census Bureau estimates and NAHB surveys indicate builders are selling a greater number of homes that have not even begun construction.
Are Higher Timber Prices on the Horizon?
As a heavily traded commodity, market prices for lumber react to a series of events on a daily basis, and the reactions may be short-lived. But the market for trees is vastly different, and it is less connected to lumber price volatility than one might think. In the US South, the inventory of standing timber has risen unimpeded since the onset of the Great Recession in 2007, which has resulted in an oversupplied market. The surplus of logs combined with improved mill efficiencies has kept log prices suppressed, even as demand for lumber surges and sawmill production continues to increase.
After dropping suddenly at the onset of the Great Recession, pine log prices have remained pretty steady across the South over the last decade. There was an uptick in prices in early 2019 that coincided with lengthy and extreme periods of wet weather, which impeded harvesting operations and put upward price pressure on supply. However, recent trends show prices in a more moderate holding pattern.
The COVID-19 pandemic continues to send shockwaves throughout the global economy, and the situation remains fluid. Trade agreements (particularly with China) are constantly evolving, imports from Canada are shifting, and regulatory uncertainty will be a concern in the near-term.
That said, the US economy will march on. Based on its deep inventories of wood raw materials, labor pools, competitive operating costs, transportation conditions, haul distances, etc., it is likely that the forest industry in the South will continue to grow and increase its share of global production volumes. Due to the South’s low log costs and deeply embedded forest supply chain, I expect this trend to continue into 2021 with a handful of greenfield lumber announcements in the region. This additional sawmill capacity will help to reduce the large oversupply of standing timber throughout the South and, in time, the rise in log consumption will begin to affect prices at the stump.
Unlike some other global forest markets that have experienced stagnation or contraction in recent years, the South is one of the hottest industry destinations on Earth, which is good news for southern landowners. In the near term, the region will continue to attract new forest industry investment, which will drive an increase in demand for its timber resources. While this new capital might not be enough to drive the kind of price spike many have been hoping for, it will be sufficient to drive slight upward price pressure while strengthening a sustainable, healthy market.