4 min read
The Graduate 2024: One Word 'Plastics', Now Two—Lignins and PEF
Jane Denny
:
Jun 6, 2024 12:00:00 AM
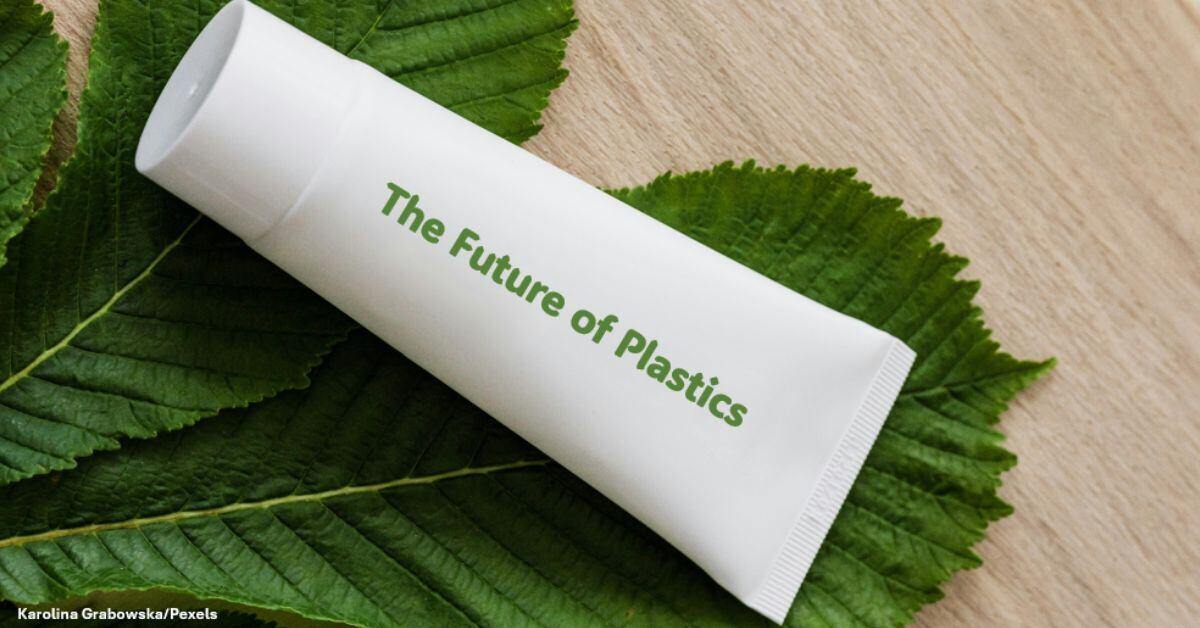
The famous line about “Plastics” from the 1967 film The Graduate, starring Dustin Hoffman as Benjamin Braddock, continues to enjoy iconic status 50-plus years on. In it, the Braddocks' family friend Mr McGuire predicts the material's great future.
What if this movie was made today? What might the wonder material of the future be? Well, lignins and PEF (polyethylene furanoate) are among the potentials. But how well-equipped are either of these raw materials when it comes to meeting the need for a sustainable plastic solution?
PEF made with the primary precursor furandicarboxylic acid and biobased monoethylene glycol (MEG) boast the profile of an entirely renewable resource.
And, if the technology is ready, when can they begin that momentous task?
PEF has high potential as a next-generation polyester polymer for use in plastic packaging. It is produced by combining monoethylene glycol (MEG) with furandicarboxylic acid (FDCA). The co-component FDCA—which acts as the primary precursor—is produced using the C6 sugars found in biomass feedstocks.
Next-generation Polymers and Feedstocks
Traditionally a fossil fuel-based product, MEG is increasingly being produced using biobased feedstocks. PEF made using these feedstocks determines its profile as a wholly renewable resources
Avantium—a renewables technology provider—expects its first commercial production of FDCA and PEF to begin this year. The firm licensed technology from US-based specialty materials company Eastman to formulate its processes for its flagship FDCA plant in Delfzijl, the Netherlands.
With a nameplate capacity of 5 ktpa, the Dutch plant will harness agricultural crops including wheat, corn and sugar beet. However, cellulose and forestry waste streams will also be used as alternative raw material sources.
Source: Karolina Graboswka via Pexels
Avantium's Ray Technology underpins a one-step hydrogenolysis process to MEG (designated plantMEG) from plant-based industrial sugars. Avantium has described its renewable MEG as competitive with fossil-based MEG.
An alternative route to PEF is synthesis via ring-opening polymerization of cyclic PEF monomers. Said to reduce reaction times and improve molecular weight control, Swiss fluid engineering firm Sulzer uses this production process.
Another Swiss company Ava Biochem derives furan-based monomers from hydroxymethylfurfural (5‐HMF)—an organic compound formed by the dehydration of reducing sugars. Yielded monomers—including FDCA—are key candidates for use in polyesters, polyurethanes and polyamides, as well as PEF products says the firm.
In April 2024, California-based carbon negative materials company Origin Materials announced the successful conversion of wood residue feedstock into sustainable intermediates at commercial scale.
The milestone was met at its Origin 1 plant in Ontario, Canada, which had been in startup mode since June 2023. Origin’s potential to help key sectors decarbonize pivots on its output of the platform intermediates chloromethylfurfural (CMF) and hydrothermal carbon (HTC). Our prior blog post Renewable Materials and the Future of Plastics explains the production processes for CMF and HTC.
The company uses locally sourced wood chips, shavings and sawdust in its Origin 1 plant. End products that can be made from its intermediate chemical outputs include textiles, plastics, tires and automotive components, fuels, and high-performance polymers, says Origin.
Performance and Life Cycle Assessment
PEF has been found to yield a plastic material with superior performance compared to PET. Its mechanical, thermal, and barrier properties surpass petrochemical-based PET in tests. However, though it is produced from 100% biobased feedstocks, it does not biodegrade in natural environments.
Industrial degradation is achievable at around 50 Celsius. Alternatively, the biological catalytic enzyme PETase is capable of breaking PEF down to its molecular level within 24 hours, says a US university team. Microbes found inside cow guts have also been found to degrade PEF efficiently.
High-profile consumer goods companies committed to PEF use include luxury goods maker LVMH for its cosmetics packaging and Carlsberg. Manufactured by bottle maker Paboco, it is being targeted at Western European markets.
FACTFILE: Sustainable Chemicals Three Pillars
Three pillars underpin the growth of technologies that rely on biomass feedstocks including lignins and PEF.
Firstly, regulatory and legislative changes globally. Governments and organizations are evolving policies to curb plastic waste and promote eco-friendly alternatives. Whether these take the form of incentives or involve prohibitive measures, they are shaping the future of plastics.
Secondly, consumer consciousness. In the US, 60% of respondents to a 2020 McKinsey sentiment survey claimed that environmental, social and governance (ESG) claims impacted their purchasing behaviors. Tracked sales growth rate over a five-year period shows shopping habits mirroring the sentiment.
Innovation in business and green chemistry values the scientific community. According to Web of Science—a 22,000-strong database of articles from peer-reviewed journals—as 2023 closed, 21,186 patents reflected lignin-focused R&D activity.
________________________________________
Lignin: A Viable Carbon Alternative..?
Lignin utilization is the significantly less commercialized of the two technologies, despite the high interest in R&D circles. A key source of organic carbon, lignins are—like rubber and starch—among Earth’s most abundant natural polymers. In nature, lignin is a natural substance that maintains plants’ structural integrity. It is a byproduct of the kraft pulping process for paper production and biofuels industry waste stream.
In paper production, it is the use of hot water and chemicals including caustic soda that breaks the bonds of wood and plants’ three main components (the natural polymers cellulose, hemicellulose, which are built from C5 and C6 sugars, and lignins). Extracted cellulose is used in downstream sectors such as textiles and, increasingly, packaging films too. Hemicellulose and lignins however, remain under-utilized resources.
In biofuel production, lignin is a second-generation ethanol biorefinery derivative that yields various aromatic and aliphatic compounds.
Currently, these processes provide millions of tons of technical lignins—the term for biomass-derived lignins—per year. However, annual availability has been predicted to be hundreds of millions of tons by 2030.
From Biomass to Car Parts
It makes sense that a compound that provides structural strength to plants and trees would find use in other applications that rely on structural integrity. A consortium of companies including UK composite, adhesive and polymer specialist firm Scott Bader and Carmaker Volvo’s subsidiary Polestar Automotive are developing car parts from lignin sources.
Automaker Ford and Origin are co-developing carbon negative car components including plastics, paints and foams. The plan is to develop an FDCA-based PEF alternative feedstock for key automotive materials.
Out of PEF and lignin, the latter is seen as potentially more sustainable due to its heightened degradation properties.
Lignin's Sustainability Profile
Lignin is considered a more sustainable option due to its heightened degradation properties. It can also be broken down (albeit slowly) in aerobic systems. PEF on the other hand—even when making use of 100% biobased raw materials—lacks the biodegradability. PEF can be recycled but then, so can many plastics made today.
Research suggests that when PEF has been copolymerized with more hydrolysable, ie. more hydrophilic and less crystalline copolymers, it will break down faster. Like much of the thought and philosophy underpinning the burgeoning lignin revolution, such innovation remains in the R&D stage.
When it comes to the candidates with profiles to match that of the wonder material plastic neither, it appears, is perfect yet. While PEF is enhanced in terms of technology readiness, its inability to biodegrade renders it as big a problem for future generations, just as plastic turned out to be.
And while lignins demonstrate great biocompatibility and end-of-life profile, its molecules are so complex that most projects remain firmly at R&D stage. For a material that scientists have known and researched for 70-plus years, success comes at a slow pace.