4 min read
Chemicals Plant Closures White Paper: A Decade of Decimation?
Jane Denny
:
Jul 19, 2024 12:00:00 AM
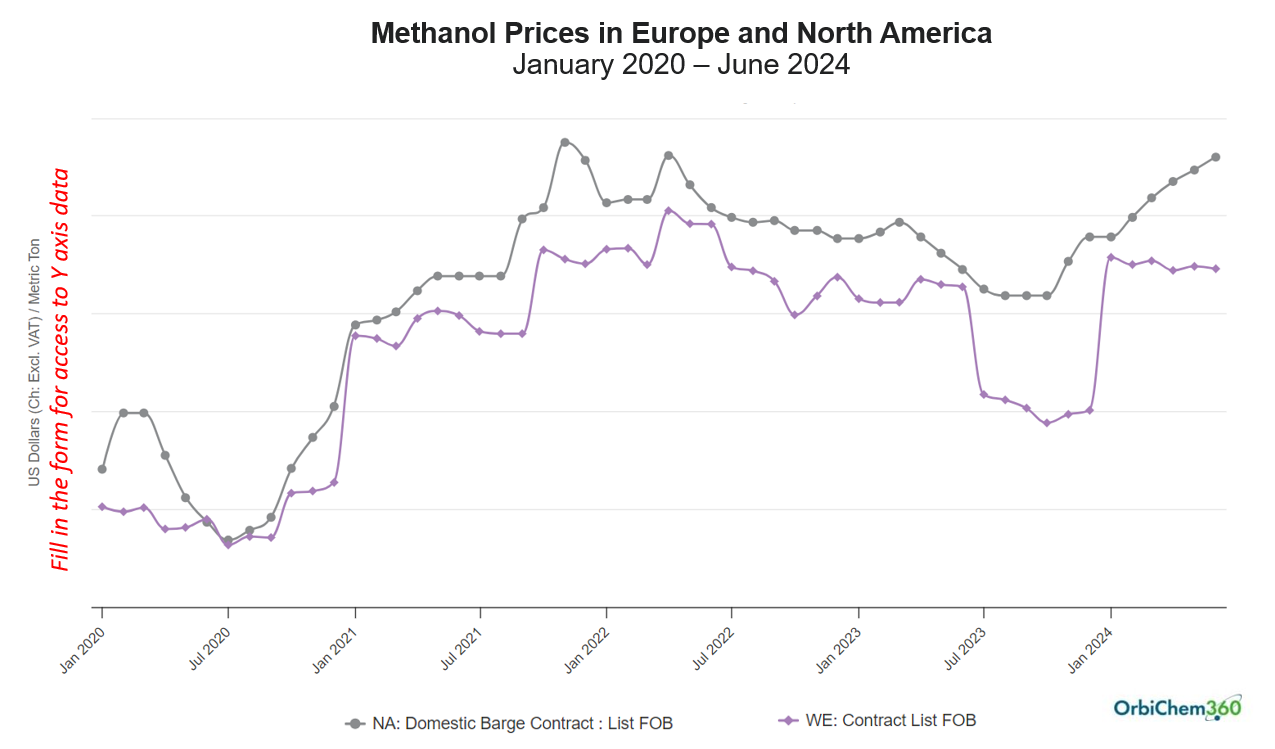
When plants producing feedstocks for intermediates and end products idle—or shut down completely—during economic downturns, the impacts are not immediately visible.
That is where the chemicals industry has been for a few years now, subject to plant closures and facility shutdowns in every region of the world. But, as market participants look to the end of 2024 for the green shoots of an inevitable recovery, shifts in the availability of key commodities and chemicals will need to be examined.
In the first three years of the 2020s—as shown in our blog post and eBook Chemicals Plant Closures in a Post-COVID War-torn World—scores of plants closed. We outlined which products and where over 10,000 kilotons per year of chemicals capacity was cut from value chains.
Polyester chain feedstocks fared particularly badly during this time, with China’s PTA output slashed by several thousand kilotons per year.
Among the significant losses to Europe’s mid-2020s chemicals output is methanol. It is a key chemical intermediate for products including formaldehyde, acrylic acid methyl ester, polyacetals, acetic acid, MTBE and plastics (PMMA). In fact, methanol is one of the world’s largest volume chemical feedstocks.
The Methanol Institute, which serves as the industry’s global trade association, says almost 100 million tons are produced annually, nearly all from natural gas or coal. To deliver end products such as paints, adhesives, plywood, clothing, and pharmaceuticals, methanol availability is crucial. Notably, Europe’s lack of competitively priced natural gas resources—especially since Russia’s supply was halted after its invasion of Ukraine—has resulted in a drastic reduction of domestic product.
Bracing for Shortages in Chemicals Value Chains
In our free-to-download eBook, we explore the reasons why the region must brace for an overall methanol shortage in the coming months and years.
Against this backdrop of reduced methanol availability, chemical sector buyers must compete with consumers in the biodiesel sector.
Methanol prices in Europe and the US are the highest available in markets. For insight on how they compare, download our plant closures eBook.
Download the whitepaper: Chemical Plant Closures in the 2020's: A Decade of Decimation?
The Alternative Fuels Data Centre explains methanol’s criticality to the biodiesel sector: For every 100 pounds (lbs) of oil or fat reacted in the presence of a catalyst—such as caustic soda—10 lbs of methanol is required. The process yields 100 lbs of biodiesel and 10 lbs of glycerine. It’s a situation Matthew Stone, VP of Business Development and Low-carbon Fuels, ResourceWise, is monitoring closely for our Prima CarbonZero business intelligence platform.
Stone says orders for methanol-fueled vessels are coming in thick and fast at shipyards worldwide. “There is less supply and potentially more demand. The carriers want green methanol, but not fossil-based methanol. Green methanol will need to be blended with fossil-based methanol to deliver a decarbonization solution at scale."
The Decline of PET Production in Europe
Another chemical sector downstream of the methanol industry is PET. It is the acetic acid that is made using methanol that goes into purified terephthalic acid (PTA), a key PET feedstock. Actually, around a fifth of global acetic acid output goes into PTA.
However, by the close of 2024, Europe’s output of the PTA will drop lower than it has been at any point during the last decade. Concurrent with Europe’s cut in capacity, the regions of South and Southeast Asia and China have significantly increased capacities, while Northeast Asia’s output—at least by the close of 2024—will show a slight decline. The scheduled closure of Mitsui Chemicals’ 145 ktpa PET resin plant in Japan in Q4 2024 is one such example of the region’s reduced capacity in the global PET market.
In fact, says South Korea-based Hyunmin Kim, Senior Consultant, ResourceWise, Chemicals, since 2013, Mitsui has endured increasing pressures on its domestic PET resin production. Kim explains that the surge in imports of competitively priced PET resin materials from overseas has eroded profitability for domestic PET resin production.
How The Supply of Key Feedstocks is Changing
Other feedstock sources Europe will see significantly reduced are ethylene and propylene. Both these commodity chemicals are raw materials within just about every single petrochemical supply chain. Ethylene is used to make paints, coatings, labels, packaging, cleaners, fibers and plastic products.
In 2019, the Gulf Petrochemicals Association estimated that 183 million tons of ethylene was produced worldwide annually. In terms of propylene exports, nearly 6 million tons was exported globally in 2023. As building block materials for products including plastics, detergents and adhesives, olefins are key to the chemicals industry.
China’s new production capacities for ethylene and propylene—developed over the past half decade—matched that of Europe’s, Japan’s and Korea’s combined. That insightful anecdote from International Energy Agency analysis encapsulates much of what ResourceWise consultants are finding out in their interactions with market participants.
Soon after announcing the start of a consultation process on its intent to close one of two polypropylene production units in Brindisi, Italy, LyondellBasell expanded its polypropylene compounding production in China.
However, expansion in North America remained in LyondellBasell’s strategy. The firm’s Channelview, Texas-based site brought up a new capacity in Q1 2023 of 470 ktpa, according to George West, the director of Chemical Intelligence—a US-based company focused on methanol, glycol, and solvents markets acquired by ResourceWise in 2023.
LyondellBasell’s output is likely to be the go-to for former Dow customers once the latter shuts down its Freeport, Texas-based propylene oxide unit at the end of 2025. Dow’s site is believed to have an output of several hundred kilotons per year.
Strategizing in an Era of Shifting Supply Chains
As the companies at the heart of the global chemicals industry adapt their portfolios around megatrends such as sustainability and considerations including "peak oil," there will be mergers, acquisitions, divestments, and carve-outs.
These change the industry inherently, or at least shift focus in some of its segments. What can appear a knee-jerk reaction to a dwindling worldwide economy might equally be a repositioning based on forward projection.
What remains vital is visibility in value chains. For the buyer, that means insight into where supply can be found at the best price when needed. For sellers, it means understanding the benchmark price for products and offering at the price point the market will accept.
Download the whitepaper: Chemical Plant Closures in the 2020s: A Decade of Decimation? to learn more.