4 min read
Biobased UP Resin: Making Thermoset Plastics Fit for a Net-Zero Future
Jane Denny
:
Aug 8, 2024 12:00:00 AM
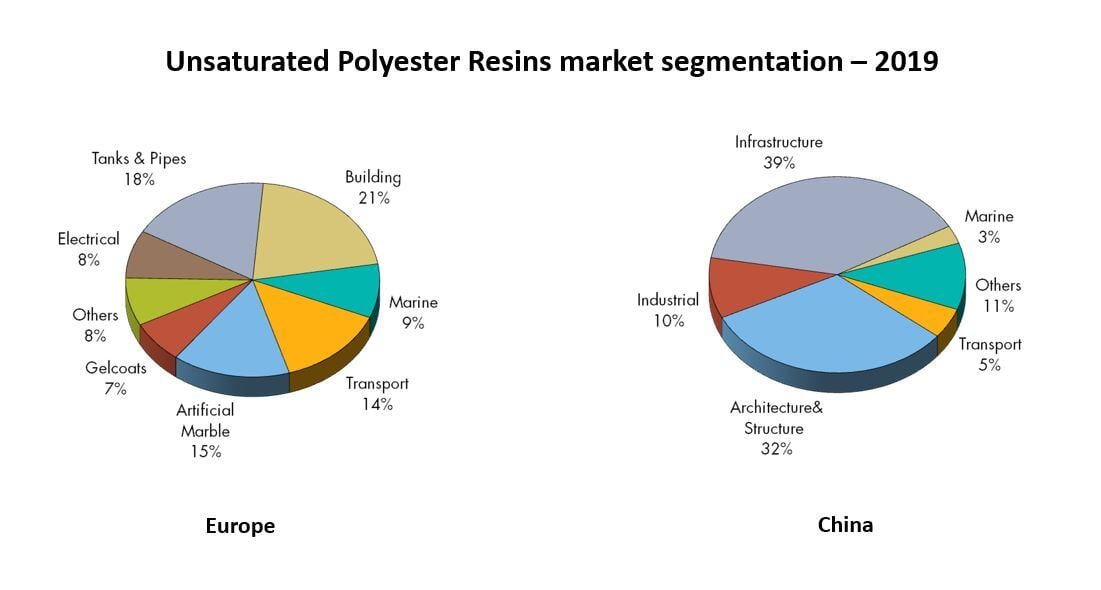
The synthetic polymer unsaturated polyester resin is used in various industrial applications and has been for nearly a century.
Durability and resistance to deterioration are among its key attributes. These properties make it suitable for applications in marine, building and construction, wind power, electrical, and automotive industries.
But as the world moves towards a sustainable future, how will this easily printable liquid polymer material evolve? To survive beyond mid-century, it must be produced using renewable resources and/or recycled content. Essentially, at their end-of-life, products made from unsaturated polyester (UP) resin must be suitable for re-use, or biodegradable.
A mass-balanced approach to manufacturing UP resin—and the intermediate chemicals it uses—is possible. But how realistic is a future without petrochemicals to provide the materials' sought-after properties?
Unsaturated Polyester Resins Applications
In automotive applications, exterior body components such as panels, hoods, and tailgates are produced with sheet molding compound (SMC), which is shaped using a compression process.
In marine applications, fiberglass-reinforced plastic boat hulls are among the uses of UP resin compounds. The production of such large items relies on bulk molding compound (BMC) processes.
The versatility of petroleum-based UP resin makes it suitable for both SMC and BMC production processes, depending on the end product's specification.
In home settings, everyday items such as bathtubs, wall paneling, and kitchen worktops are made from UP resin, meaning few humans are ever far from its end-use products.
When it comes to the municipal infrastructure serving homes, it is often UP resin cured-in-place-pipe (CIPP) linings that underpin the effectiveness of drainage and sewerage systems. Suffice to say, it is difficult to imagine our world without this useful material.
A Fossil Fuel Driven Chemicals Subsector
Traditionally, the raw materials used to make UP resin have all been petroleum-based. These include maleic anhydride, phthalic anhydride, propylene glycol (also known as monopropylene glycol), and diethylene glycol (DEG). The aromatic compound styrene monomer is typically used to enhance polymerization in the production process.
However, there have been advances in the production of circular UP resin products. Ineos Composites claims its Envirez product is “the world’s first commercially available UP resin containing a significant quantity of renewable materials”.
According to Ineos, Envirez products incorporate a variety of renewably sourced raw materials and 13% recycled material content.
The product line—which Ineos acquired from Ashland Global Holdings in 2020—is used in various applications. Examples include the bodywork panels of John Deere farm equipment (made using the SMC process) and in a high-performance test boat from the recently closed British Columbia-based boat manufacturer Campion.
German chemicals manufacturer Schill + Seilacher "Struktol" offers a bio-resin UP resin. The product—designated polyvertec—comprises almost 100 percent biobased raw materials. Not only does the product’s mechanical properties match those of standard polyester resins, but it is also suitable for both SMC and BMC processes. It is also suitable for pultrusion—the manufacturing process in which fiber reinforcements and resin matrices are pulled through a die to create composite parts, including bridge components.
Industry View on Biobased UP Resin
Sam Uctas, Consultant ResourceWise Chemicals, believes that the nascency of the biobased UP resin market and the limit to commercially available products is key. However, at present, there are no policy drivers for its use in the market either.
“Because the use and inclusion of biobased UP resin in products doesn’t offer cost effectiveness, UP resin with a sustainable profile will likely only become prominent when environmental regulations are imposed."
While, there has been an increase in the amount of eco-friendly styrene available during the past few years, says Uctas, "it remains very niche".
"Really, biobased styrene is only bought when the environmental impact of the product is especially important to the buyer. Generally speaking, biobased UP resin receives little attention in the current market. This is largely due to margins already being squeezed by depressed European and Chinese markets.
“This is likely to remain the case until bio-alternatives become more economically viable and regulations involving them become more commonplace,” adds Uctas.
Innovations in Biobased UP Resin
US Army and Drexel University scientists codeveloped vinyl ester and unsaturated polyester composite resins over a decade ago. They synthesized isosorbide-methacrylate by the direct esterification of isosorbide, a reactive monomer, and a base catalyst.
The ensuing scientific paper found that the non-petroleum cellulose or carbohydrates-based product had “good potential for use in composite applications where a moderate to high temperature free radical cured polymer matrix is needed.”
A more recent scientific paper explored UP resin production using itaconic, succinic acid, and isosorbide as raw materials. Isosorbide is a derivative of glucose sorbitol, which is obtained from starch, sucrose, or cellulose feedstocks.
The team showed that the use of specific polyols influences UP resin properties. Biobased UP resins containing ratios of propylene glycol (PG) and neopentyl glycol showed good mechanical properties.
Thermo Scientific—formerly Acros Organics—supplied biobased PG and neopentyl glycol for the study. Overall, the team reports that the study showed the alternatives to have great potential as petroleum-based resin substitutes.
“Generally, the properties of the investigated biobased UP resins can be fine-tuned by the proper selection of glycols in the prepolymer feed.
The study found that isosorbide significantly increases the resin stiffness, and neopentyl glycol impacts the resin’s flexibility and elasticity.
Commercial Consortium
Due to the complexity of UP resin's chemical structures, the material cannot be melted for recycling and reuse as is possible with many other plastics. Consequently, over 40 percent are burned in incinerators, and over a quarter end up in landfills, according to estimates from German research organization nova-Institut.
To combat this, a consortium of Spanish companies funded by the country’s government explored renewably sourced polymeric resins and processes for recycling and reuse of residues.
The EOCENE project was mandated to develop, validate, and characterize new resins using bioresources through enzymatic and chemical approaches. The goal was to develop monomers and precursors using vegetable oils and waste from the agricultural and food industries to produce fully biobased UP.
Net Zero Future Goals
With the world's net zero aspirations becoming ever more vital to a sustainable future, plastics that draw on fossil fuel resources occupy an increasingly precarious position.
Resin-based plastics remain vital to modern life, but finding ways to make them from renewable products is critical. Once the industry has the solutions to deliver sustainable products, policy levers must be put in place to incentivize their use.