4 min read
Biobased, Recycled and Renewable Carbon Chemicals: An Introduction
Jane Denny
:
Jul 31, 2024 12:00:00 AM
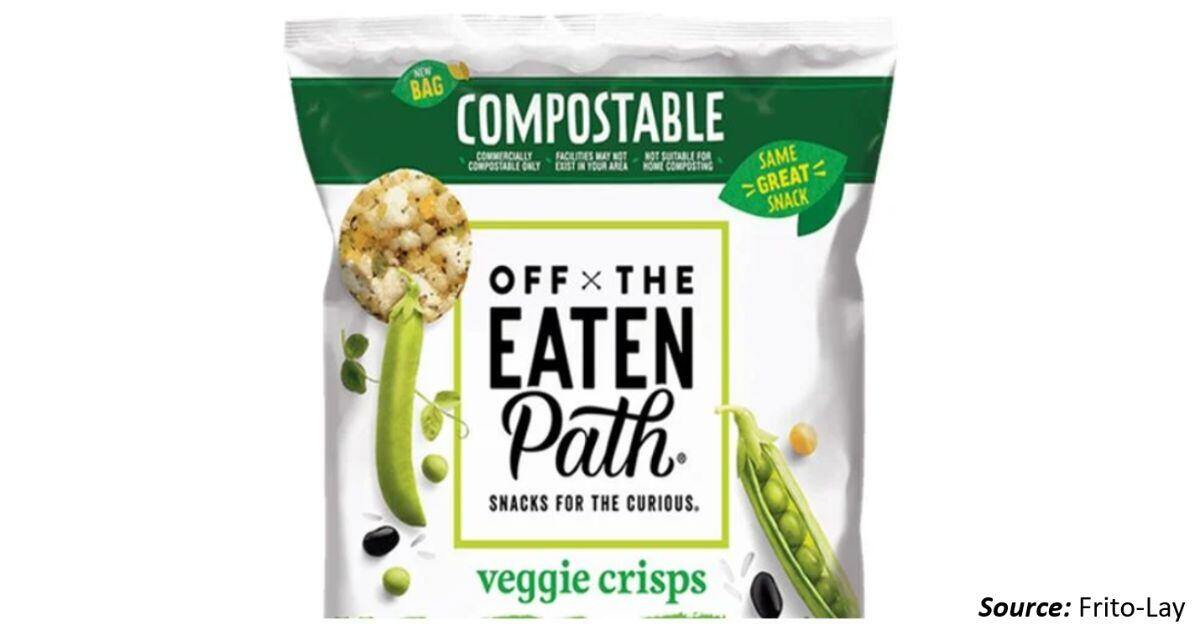
Biobased products are defined as having been made from biological—meaning living—or renewable resources. They include corn, sugar cane, cellulosic, vegetable oils, and even the exoskeletons of insects or cell walls of fungi. All of these resources can be converted into valuable feedstocks and products.
What sets biobased materials apart is that they rely on new carbon sources for their raw materials instead of fossil fuels' old carbon resources.
The overhaul of transport fuels—for example, by developing biomethane for shipping, biodiesel for cars, and sustainable aviation fuel—is designed to cut greenhouse gas emissions.
Spurring a circular economy where plastics are made with recycled or biomaterials may reduce landfill waste. Transforming waste materials into feedstocks for manufacturing will reduce our dependence on oil and gas reserves. These are the cornerstones of the net zero future our world needs to survive and thrive.
Nature-based Feedstock Potential
One process for creating sustainable materials is to build on naturally occurring biomass. Rayon textile fiber, for example, is largely made from wood pulp-derived cellulose. And cellophane film has been made using wood pulp for more than a century.
Using wood-based feedstocks for products in a biobased economy is a good idea for many reasons. On a per-hectare basis, the eucalyptus tree yields around ten times more raw material than a cotton plantation. An adult pine tree can be grown in the US south in 40 years.
Another solution is producing polylactic acid (PLA) resins from lactic acid. Potential sources include corn and bagasse—the pulp that remains after the juice is extracted from sugar cane or similar plants. Frito-Lay Off the Eaten Path veggie chips, for example, are sold in bags that are 85% polylactic acid.
Most potato chips, crisps, and snack bags are made using a combination of polypropylene, polyethylene, and thermoplastic resin. According to Statista, over a hundred million Americans consume 4-7 bags per month, a great deal of petroleum-based packaging in just one country worldwide.
Cellulose Acetate Plastics
Using cellulose acetate (CA) to make plastics is also a potential solution to the environmental problems created by traditional plastics. Disposable containers for ready meals are currently made with fossil fuel-based plastics and phthalate plasticizers. Replacing the petrochemical polymer plastic with CA and using food-grade plasticizers—made from sorbitol or glycerine, for example—could revolutionize the ready-meal packaging sector.
CA can also enhance the bio-content of petrochemical-based plastics even if it does not entirely replace them. Using a percentage of CA as a drop-in raw material presents a part-biobased product. These products have an overall more sustainable profile.
However, an advantage of fully CA-based plastic products is that they are biodegradable. Scientists at Woods Hole Oceanographic Institution scientists showed CA's accelerated propensity to degrade in ocean environments.
Using CO2 To Make Consumer Products
German company Covestro—a spin-out from multinational biotech firm Bayer—makes the key intermediate isocyanate from carbon dioxide (CO2). Yes, that's correct. The molecule responsible for global warming can be used in everyday products like mattresses and shoe soles.
Covestro's isocyanate precursor—designated cardyon—is made via by the catalysis of CO2 and propylene oxide. The process yields a new type of polyol with a CO2 share of up to 20 percent. First used for flexible foam products, including mattresses, it is now used by FoamPartner (recently acquired by Texas-based chemicals manufacturer Carpenter) to produce components for automotive interiors.
UK-based chemical manufacturing company Econic Technologies transforms waste CO2 into high-performance materials. Like Covestro's cardyon, Econic's proprietary technology can be used in automotive, furniture, apparel or coatings, adhesives, sealants, and elastomers, otherwise known as CASE applications.
Renewable Platform Chemicals Potential
Producing renewable platform chemicals from the derivatives of these new carbon sources not only affords end products a built-in biodegradability, they can be low priced if the raw material supply is plentiful and the supply chain robust.
Sound environmental credentials are their major benefit today and a significant reason for the growing interest in them as companies work to improve their Environmental, Social, and Governance (ESG) profiles. It is ideal for drop-in biobased monomers to match their synthetic equivalents. It is largely considered that when they do, the price of end products can be increased by up to 20 percent.
Take the Charlie sneaker from Louis Vuitton, for example. ResourceWise explored the renewable and recycled profile of this US$780 product in a prior blog post, Recycled Synthetics Vs. Renewable Fibers: Balancing Sustainability.
Biobased Routes to Existing Intermediates
Developing biobased routes to existing intermediates is an increasingly attractive proposition for brands keen to limit fossil-based feedstocks. If they are identical to the petrochemical-derived chemicals they replace, biomass-derived replacements can be perfect replacements
Biobased processes to make chemicals, including paraxylene, adipic acid, butadiene, and caprolactam, have all been developed in the past decade.
For example, using lumber and wood chip feedstocks, California-based company Origin Materials produces 100 percent biobased paraxylene and purified terephthalic acid. With these materials, bio-polyethylene terephthalate (Bio-PET) can be made.
Bio-PET is a recyclable intermediate product made from renewable raw materials. It is a drop-in bioplastic, meaning it can be introduced to production lines with no changes to process necessary.
Last year, Mitsubishi Corporation, Suntory Holdings, and ENEOS unveiled a plan to build a supply chain for sustainable biomass-derived PET bottle production. Drawing on materials including used cooking oil from Finnish oil refining firm Neste and applying a mass balance approach, the trio aimed to deliver bioparaxylene in 35 million PET bottles by the end of 2023.
Innovation Brings Useful Feedstocks
Chemically, sugar consists of carbon, oxygen, and hydrogen atoms, with glucose and starch being among the most abundant sources.
Conventionally, the chemical compound isobutanol—used in coating resins and solvents—is derived from propylene. However, the same molecule can also be derived from sugars.
Colorado-based renewable chemicals and advanced biofuels company Gevo is converting biobutanol to SAF. Alongside its output of ethanol from corn residues, Gevo has produced bio-isobutanol at its Minnesota facility for a decade.
Collaborating with scientists from the Technical University of Munich, a University of Queensland research team engineered an enzyme to produce ten times the amount of isobutanol yielded via traditional cell-based biomanufacturing methods.
A Bioeconomy in Development
The transition from fossil fuel-based to biobased, recycled, and renewable carbon products is increasingly being considered a key solution to humanity's basic challenges.
Managing climate change, preserving vital biodiversity, and food security all pivot on considered approaches to energy and raw material provision.
Sustainability is not an explicit concept. Each region of the world will take a different journey to lower emissions and successfully harness available feedstock and/or waste streams.
Biomaterials are one part of the big picture. Recycled and renewable carbon raw materials will also play a role in the journey to a net zero future.