3 min read
Biobased Chemicals Knowledge Base: From Zero to Hero in Minutes
Jane Denny
:
Nov 27, 2024 12:00:00 AM
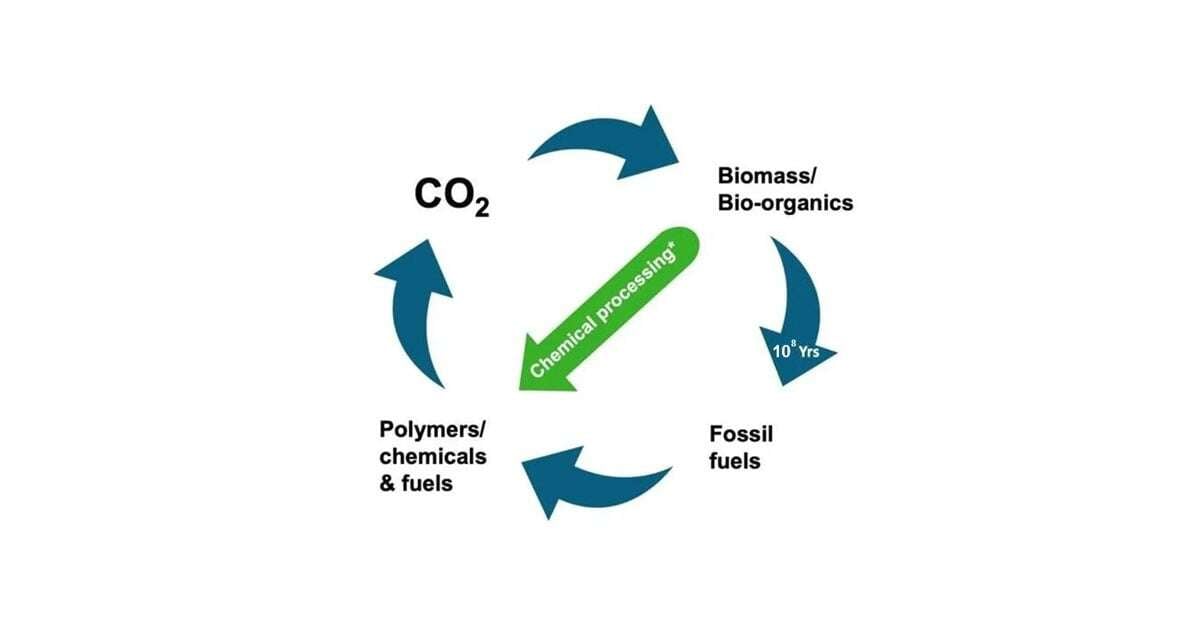
Biobased and circular economies have emerged as globally impactful transformative forces in industry this decade.
On the demand side, there is a transformative force for consumption changes and waste reduction. Consumers are turning their backs on plastics, such as packaging, that risk adding excessive waste to the environment.
As political leaders and authorities build upon and tighten the laws and regulations that govern the manufacturing industry, the renewable and recycled content of products will increase.
Policy is increasingly supporting brands that demonstrate Environmental, Social, and (corporate) Governance principles in a bid to protect our world and future.
The movement is destined to place a greater focus on localized production, as opposed to goods being shipped around the globe, adding to its carbon footprint. Local feedstocks will be favored in the production of biobased chemicals and materials. Where renewable feedstocks are less available, for example due to a lack of land, plastic waste will need to be collected. Programs are needed to encourage municipalities to sort waste.
Biobased products are defined as having been made from a biological—meaning living—or renewable source. They include, but are not limited to corn, sugar cane, cellulosic, and vegetable oils. Even the exoskeleton of insects and cell walls of fungi—otherwise known as chitins—can be made into useful feedstocks and products.
What sets biobased materials apart is that they rely on new carbon sources for their raw materials, as opposed to the old carbon sources of fossil fuels.
One process for creating biobased materials is to build on naturally occurring materials like rayon fiber, which is largely made from wood pulp-derived regenerated cellulose. In fact, the production of cellophane film using wood pulp has been practiced for more than a century. And with good reason.
Pine and spruce species trees, which grow in North America, Europe, Asia, and Australia, mature in 40 to 50 years. Slower-growing tree species can take a century to reach adult size. Compare this to the millions of years it takes to cultivate fossil fuel feedstocks. Bio and forest-based starting materials are compelling alternatives.
The eucalyptus tree, for example, is a highly valued raw material for pulp and paper manufacturing. The Australian native globulus Labill (Tasmanian blue gum), characterized by fast growth yields, takes just ten years to mature and produces around ten times more feedstock than a cotton plantation. Both cotton and eucalyptus feedstocks are used to make some specialty paper products.
Source: US Dept. of Energy and ResourceWise
Polylactic Acid Economics
Polylactic acid (PLA) resins demonstrate similar properties to polystyrene and polypropylene. A polyester made using lactic acid, PLA's raw materials include corn and bagasse.
Bagasse is the the pulp that remains after the extraction of juice from sugar cane or similar plants. Students from the Northeastern University College of Engineering in the US investigated several PLA raw materials. The found corn, as per this presentation, cost $0.06/lb, with bagasse just a fraction higher. Other sources— coffee beans, for example—have also been investigated as a PLA potential source.
Ideally, drop-in biobased monomers match their synthetic equivalents. A price hike of up to 20% may be accepted if ESG value is demonstrable
Similarly, potato peel waste is seen as a potential PLA raw material. More commonly used in animal feed and fertilizer markets, the group estimated that globally, waste peel from potato chip processing plants totaled over 18 million tonnes of potential. The group reports that producing PLA resin from potato peel waste based on its 15% starch content could prove a viable alternative to fossil-based plastics.
Cellulose Acetate Plastics
Cellulose acetate (CA) plastics could be a potential solution to the environmental persistence created by traditional plastics. They are biobased plastics with superior properties. The properties of the materials can be fine-tuned by adjusting the plasticizer level. CA can be effectively processed using food-grade plasticizers instead of phthalate-based plasticizers. CA can also enhance the bio-content of petrochemical-based plastics.
A biodegradation profile for CA gives the material a particularly refreshing spin. Scientists at Woods Hole Oceanographic Institution uncovered an accelerated propensity to degrade in ocean environments.
The acetylation process that yields cellulose acetate involves replacing the hydrogen atom of a hydroxyl group with an acetyl group.
Producing renewable platform chemicals from the derivatives of these new carbon sources not only affords end products a built-in biodegradability, but they can also be low-priced if the raw material supply is plentiful and the supply chain robust.
A sound environmental footprint is the major benefit today and a significant reason for the growing interest in them. Companies can improve their ESG profile by using cellulosic feedstocks and raw materials in their products.
Drop-in Chemicals
Developing biobased routes to existing intermediates is an increasingly attractive proposition for brands keen to limit fossil-based feedstocks. Because they are identical to the petrochemical-derived chemicals they replace, biomass-derived replacements are known as drop-in chemicals, representing a perfect replacement. Isobutanol, which is used in coating resins and solvents, is conventionally derived from propylene, but the same molecule can also be derived from sugars.
Biobased processes to make chemicals, including monoethylene glycol (MEG), paraxylene, adipic acid, butadiene, and caprolactam, have all been in development within the previous decade.
With European Union funding, Dutch firm Avantium developed a single-step process to turn industrial sugars into plant-based MEG. Before Avantium’s breakthrough, biobased MEG production necessitated chemical steps so inefficient and expensive compared to fossil-based routes, industry largely rejected the product. Hydrogenolysis relies on catalysis to break the chemical bond in the organic molecule while simultaneously adding a hydrogen atom to the molecular fragments yielded.
In terms of its carbon footprint, life cycle analysis demonstrates a CO2 emission reduction of 56 to 83% compared to MEG derived from petrochemical sources, according to Avantium. Construction of the company’s North Belgium-based plant began in 2018 and is expected onstream in 2024.
The final option is to create completely new biobased polymer products that demonstrate similar or improved properties compared to existing commercial oil-based products.
Stay up to date by subscribing to our newsletter.