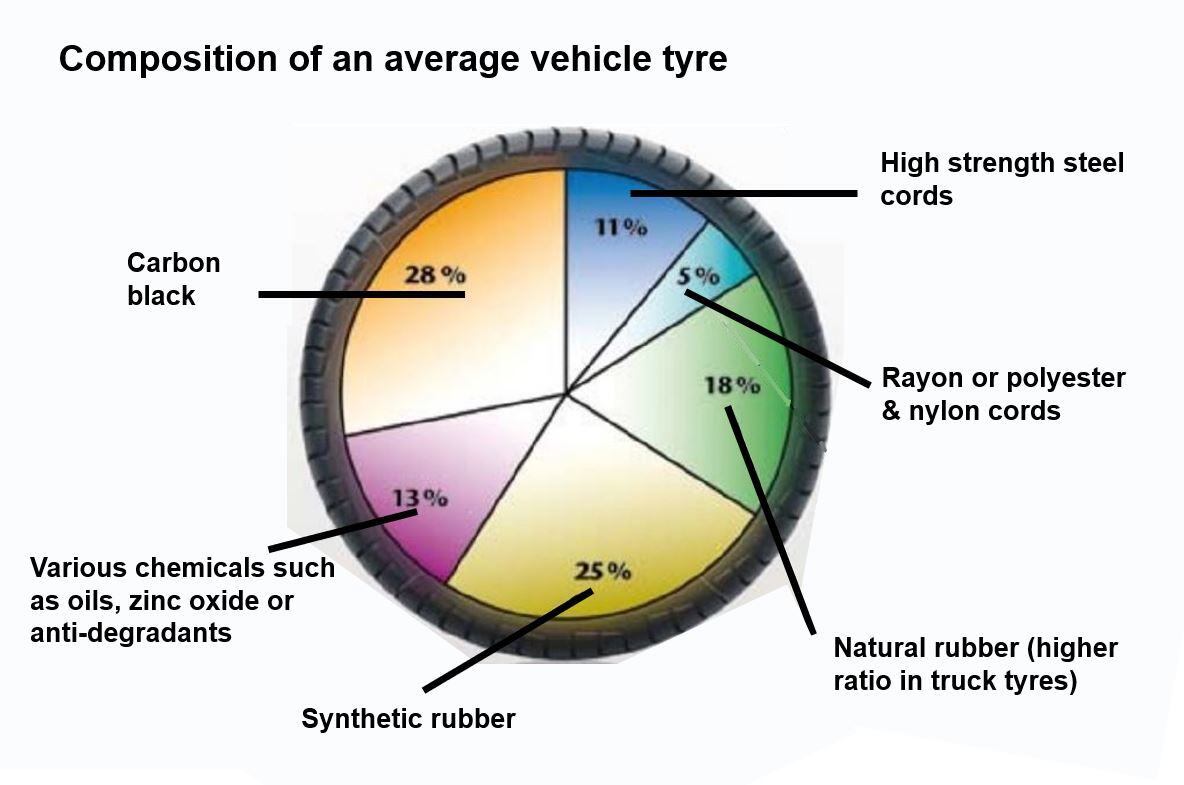
Automotive industry participants have made great strides in improving the sector's sustainability profile since the 1990s. In fact, catalytic converters have cut vehicular pollutants so effectively that the volatile organic compounds in a can of deodorant or hairspray are now more cause for concern.
That said, tire manufacturing remains an area ripe for disruption. US-headquartered research organization Smithers predicts that the total weight of new tire output in 2024 will be nearly 23 million tons. The figure represents a 3.4% compound annual growth rate from 2019.
To put that in perspective, the World Business Council for Sustainable Development estimates that around a billion tires reach their end of life each year—the majority sent to landfill. And even more new tires than that are produced on an annual basis. And still, petrochemicals underpin the majority of tire sector output.
Tire materials include a mix of a dozen synthetic and natural rubbers, which account for almost half of the tire by weight.
Eight types of carbon black are used in the end product. There has been a trend toward the use of recovered carbon black, a solid carbon residue from tire pyrolysis. Nylon, polyester, steel, and chemicals, including waxes and oils, make up the rest.
Source: ResourceWise
Engineering Thermoplastics in Automotive
Polyamide tire cord is a vital component in most tires. Polyamides’ distinct mix of properties—from elasticity to the strength of steel—make it suitable for this demanding application. The engineering plastics’ resistance to heat, oil, petrol, acids, and alkalis make the polymer suitable for demanding applications.
Polyamide gives bias ply tires their reinforcement framework, making them capable of withstanding harsh conditions. The engineering thermoplastic gives strength to the tire shell, fortifying it from the inside. Polyamide tire cord fabric is also a good bonding substrate for the rubber and carbon black filler that encase it. Bias ply tires generally use durable high-tenacity filaments such as polyester, rayon, and polyamide.
Recycled polyester fiber tire cords have been around since the early 2000s. In 2022, Japanese chemicals manufacturer Teijin developed a resorcinol formaldehyde-free adhesive tire cord using a chemically recycled polyester fiber for rubber reinforcement.
French tire maker Michelin teamed with biochemistry company Carbios to develop a high-tenacity PET fiber for tire cords. Using Carbios' innovative enzymatic recycling process, waste PET plastics and textiles such as beverage bottles and polyester clothing are depolymerized. The process allows all types of PET waste to be recycled to 100 percent recycled and 100 percent recyclable PET products without loss of quality, says Carbios.
Carbon Black: Fossil to Renewable Raw Material
According to Mitsubishi Chemical Holdings Group (MCHG), the global carbon black market will be worth $26bn next year. However, the sector's primary source is fossil fuel resources. Producing a ton of carbon black uses 1.5 tons of fossil feedstock and vast amounts of water. It also releases up to three tons of CO2 emissions.
US-based sustainable technology company Origin Materials is converting its wood residue-derived hydrothermal carbon (HTC) into specialty carbon black material for tire applications.
There are a number of projects that aim to bring circularity to the tire sector by recycling old tires to produce secondary raw material (SRM) for newly manufactured tires.
Black Carbon Circularity
A consortium including global specialty chemicals manufacturer Orion and French tire manufacturer Michelin investigated steps to deliver sustainable carbon black. The EU-funded project involved the development of tire deconstruction and granulation using Michelin machinery, as well as pyrolysis and oil distillation steps.
The end-of-project report advised that "industrial scale-up required policy and regulation designed to increase investment in the tire-to-tire recycling industry and encourage profitability during production ramp-up."
Another EU-supported endeavor—the CBreCYCLE project—delivered recovered carbon black at less than 0.5 tons of CO2 per ton. The team used a pyrolysis system developed by Polish firm Syntoil through the project and a novel approach to purification.
Meanwhile, another Polish company, Contec, is developing tire recycling technology in collaboration with industrial partners and the Warsaw University of Technology.
Contec's process includes recovering steel cords, which make up about 15 percent of the overall weight. Added to tires to increase their mechanical strength, the recovered steel is re-usable as an insert for new tires. The rubber element is converted to granules.
According to Contec, more than half the pyrolysis oil Contec's process yields contains aromatic hydrocarbons. A significant amount of carbon is recoverable from the natural rubber input. The carbon footprint of the technical carbon black recovered by the process is over 80% lower than traditional production routes to carbon black.
Bio-butadiene: Realizing Renewable Rubber
A copolymer made from the monomers of styrene and butadiene, styrene-butadiene rubber is the primary material combined with natural rubber to make tires.
Alternatives to petrochemicals, such as styrene and butadiene, are in development. Polish chemical company Synthos and Global Bioenergies—based in France—collaborated on an enzymatic dehydration process for bio-butadiene. Following the pilot stage success, Texas-based licensing company Lummus joined forces to start next-level technology development.
US-based manufacturing company Trinseo partnered with Netherlands-based chemicals manufacturer ETB Global BV to commercialize biobased butadiene using ethanol feedstock.
Earlier this year, Michelin, IFP Energies Nouvelles, and Axens inaugurated an industrial-scale demonstration plant for biobased butadiene. Located in France, the the demo plant follows several years of lab work and a pilot production of hundreds of grams of bio-butadiene.
Renewable Functional Fillers
Around 70% of the world's carbon black output is used as a reinforcing filler in tires. With this in mind, UPM Biochemicals developed a new category of functional fillers. The innovation replaces the fossil-based carbon black—over a quarter of tires' composition—and precipitated silica.
UPM's 100% wood-based BioMotion Renewable Functional Fillers (RFF) will be produced in Leuna, Germany. Monoethylene glycol, monopropylene glycol and RFF from sustainably-sourced and certified hardwood.
Automotive Supply Chains of the Future
The auto industry is in the midst of the greatest transformation since Henry Ford first conceptualized the Model T over a hundred years ago. OEMs and supply chain participants are overhauling their supply chain and raw material sourcing strategies.
As tire makers worldwide set goals for renewable content, buyers and procurement teams need insight. ResourceWise price indexes and forecasts, analysis and trade flow datasets cover a wide range automotive supply chains. Whether it is composite materials for under the hood applications, inner vehicle comfort and style or bodywork, our portfolio has it covered.
Our business intelligence platforms unravel the automotive sector from materials and fuels angles. See what we offer by scheduling a demo with one of our experts.