5 min read
Acetone Innovation: A Revival of 20th Century Technology
Jane Denny
:
Sep 13, 2024 12:00:00 AM
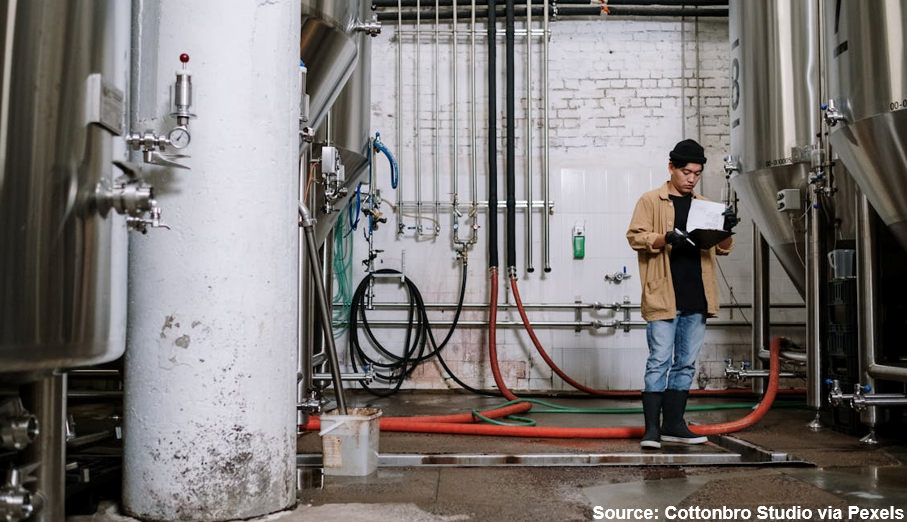
During the course of 2024, more than 8,000 kilotons of the building block compound acetone will be used in fuels, acrylics, fabrics, cosmetics, and the personal care industry. In fact, the annual market for acetone and its co-chemical isopropanol is estimated to be around US$10 billion.
Acetone is a by-product of phenol in the cumene process—also known as the Hock process—and its output relies on fossil fuels. It is, therefore, innately unsustainable.
Not only do credible models for biobased routes to this chemical intermediate exist, but non-petrochemical production was achieved across the UK and North America for decades.
As referenced in Part 1 of this blog series, a pioneering fermentation procedure introduced in the early 20th century was widely used until the 1930s. The acetone–butanol–ethanol (ABE) process developed by Russian biochemist Chaim Weizmann—widely considered the 'father' of industrial fermentation—converted corn and potato starch to acetone and butyl alcohol using bacteria.
Weizmann may not have foreseen relegation for his sustainable microbe-based solution as cheaper petroleum-derived routes emerged. Nor could he have known his approach would resurface alongside other non-fossil fuel-based processes in the new millennium.
Sustainability in 2010s: Thwarted Intent
It is usual for alternative raw materials to gain market traction when crude oil prices rise, and ABE production didn’t vanish entirely after the 1930s. ABE plants remained onstream in South Africa, Japan, China, Europe, and East Asia until the 1980s.
And in the last decade, a UK company secured $100 million in funding to revive ABE-based production in the west. In fact, Green Biologics was all set to disrupt the petrochemical-based acetone market with its renewable modified microbe-based alternative.
However, in 2019—three years after coming onstream—Green Biologics wound down. Its flagship facility in Minnesota was shut down due to the lack of funding needed to scale up and grow sales.
It marked a disappointing outcome for a promising technology, an outcome that wasn't exclusive to western regions. Chemical manufacturing company Cathay Industrial Biotech—based in Jilin, China—was among a handful of Chinese companies that had realized, or plans for, ABE production capacity a decade ago.
By 2015, each had shut down or abandoned the strategy. Cathay's decision pivoted on the country's corn (maize) prices having suddenly doubled. But, as happened with the promising renewable feedstock biosuccinic acid a decade ago, interest in ABE waned when oil prices dropped to levels that restored fossil-based intermediates’ cost-effectiveness.
From Waste Gas to Useful Platform Chemicals
There is a strong analogy between the ABE and the processes developed by US carbon recycling company LanzaTech.
Both employ anaerobic fermentation technology using a bacteria of living beings, clostridia—֫though LanzaTech’s rabbit-sourced version does not sporulate (produce its own spores). LanzaTech's transformation of pervasive carbon emissions into feedstock is what really makes its innovation stand out. ABE’s feedstock is sugars such as corn syrup, sugarcane and fructose.
Illinois-based LanzaTech has already proven that microbe-driven technology can produce chemicals currently made using petroleum feedstocks. The technology benefits from its use of waste gases—such as industry emissions and biomass-based syngas—as feedstock, as opposed to the food sources used in ABE production units.
LanzaTech has proven its innovation for acetone production at pilot stage. In a Nature journal study, Carbon-negative Production of Acetone and Isopropanol by Gas Fermentation at Industrial Pilot Scale, a research team compared the emissions of its process to traditional petroleum-based methods. LanzaTech's process locks in 1.79kg and 1.17kg of CO2 per kilogram of acetone or isopropanol, respectively. This is the post-offset of process carbon emissions. By contrast, just one kilogram of acetone produced with fossil fuel-based feedstocks emits the equivalent of 2.55kg CO2, according to the report.
Last year, LanzaTech and Abu Dhabi National Oil Company (ADNOC) partnered to realize aspirations including carbon-negative acetone and isopropanol. ADNOC’s carbon monoxide, hydrogen, and carbon dioxide waste streams will be used to deliver commercial-scale output.
With ADNOC's expected acquisition of German plastics producer Covestro, the LanzaTech partnership is a keen fit. Covestro uses CO2 to manufacture the transparent engineering thermoplastic polycarbonate, and isocyanates—the precursors for polyurethanes.
Not only is waste CO2 locked into the product—as opposed to being released into the atmosphere—up 50 per cent of fossil raw materials can be saved in the production process.
Optimizing Efficiency in Industrial Fermentation
As per the economics of all product yield R&D, achieving high concentrations of selected molecules lowers the cost of downstream separation and purification. With this in mind, Delft University of Technology scientists set about improving isopropanol and acetone concentrations in their own pilot scheme fermentation mixture.
One of their approaches involved the novel separation method known as pass-through distillation—a relatively cost-effective process due to low delivery temperatures.
The Delft team’s paper, Advanced Purification of Isopropanol and Acetone from Syngas Fermentation, outlines outcomes using a pilot process similar to LanzaTech’s. It was published in the Journal of Chemical Technology and Biotechnology in December 2023.
Downstream of Acetone
The largest use of acetone is in the production of bisphenol A (BPA). Made from acetone and phenol catalyzed by hydrochloric acid or sulfonated polystyrene resin, BPA is an intermediate in epoxy and polycarbonate resins manufacturing. Polycarbonate resin use has increased rapidly in recent years, with BPA manufacturing sites increasing in China in recent years so as to ensure the engineering thermoplastic has ample feedstocks.
One of the largest markets for acetone is for manufacturing the intermediate methyl methacrylate (MMA), mainly produced via the reaction of acetone with hydrogen cyanide. An important monomer, it is used mainly in the production of acrylic sheeting, molding powders, resins and surface coatings.
Polymethyl methacrylate (PMMA) is a polymer of MMA—a lighter, shatter-proof glass substitute. The transparent protective screens—used universally during the COVID-19 pandemic—are made using acrylic sheets of PMMA. Brand names for the product include Plexiglas, Perspex, Acrylite, and Lucite. PMMA is also used in car windows and headlamps.
Source: ChemEdge360
Acetone Trade and Capacity Snapshot
According to the ResourceWise chemicals intelligence platform ChemEdge360, Saudi Arabia, Spain, and Singapore are among the world’s major exporters of acetone. The graphic above shows a customized version of ChemEdge's acetone-focused Capacities portal Trade Flow visual datasets.
Despite having over a third of the world’s total acetone production capacity located in China, the country exports relatively little product. In addition to its domestic output, the republic relied on significant import volumes—in the several hundreds of kilotons range—in 2023. Chinese imports of acetone came from countries including Saudi Arabia, Taiwan, South Korea, and Thailand.
Around 12 per cent of global capacity is located in North America. In 2023, export volumes out of the US were almost 100 ktpa, mostly to Canada. The country also imported over 50 kilotons during the year.
European companies account for 16 per cent of worldwide production capacity. Spain exported over 150 kilotons in 2023, while Finland exported almost 100 kilotons. Most of their exported product remained in the region.
Acetone: A Cheap Innovation?
Researchers from Brazil and Germany developed a method that uses only light and photoactive iron chloride—an inexpensive chemical compound.
According to the study, irradiating chloride at certain wavelengths produces radical chlorine, a potent oxidant that activates the C-H bond and yields acetone in the presence of oxygen.
What makes the process cost-effective is that it eliminates the need for propylene production at intermediate stages. That reduction in process steps means it consumes less energy, as does its reaction at room temperature. The study concludes that iron-based C–H activation is a “holy grail” of modern chemistry. “In the best outcome, 100 per cent conversion of propane with 69 per cent selectivity in acetone was achieved after four hours of irradiation under violet light.”
“Synthesis of valuable chemical feedstocks, including acetone and acetic acid, under very mild conditions holds promise for the development of sustainable industrial conversions of hydrocarbons,” it adds.
Managing Push and Pull Market Dynamics
Producing acetone from biomass and waste residues has the potential to reduce market volatility. It removes the control over prices currently exerted by the crude oil industry, where the cost of a barrel of oil is subject to extreme volatility (As demonstrated in the price index graph below).
Source: ChemEdge360
Additionally, petrochemical-based feedstocks and their downstream products will increasingly come up against policy designed to eliminate them. The EU’s Carbon Border Adjustment Mechanism (CBAM) for example, has been designed to incentivize the EU’s global trading partners to decarbonize their manufacturing industries.
The European Parliament has already indicated intent to expand the scope to include plastics and chemicals by 2026. These types of environmental regulations are limiting the petrochemical sector’s relevance. Though it will take time, these policies will ultimately facilitate the growth of the renewables sectors.
Explore the 100-plus chemicals we cover and the industry sectors they serve.
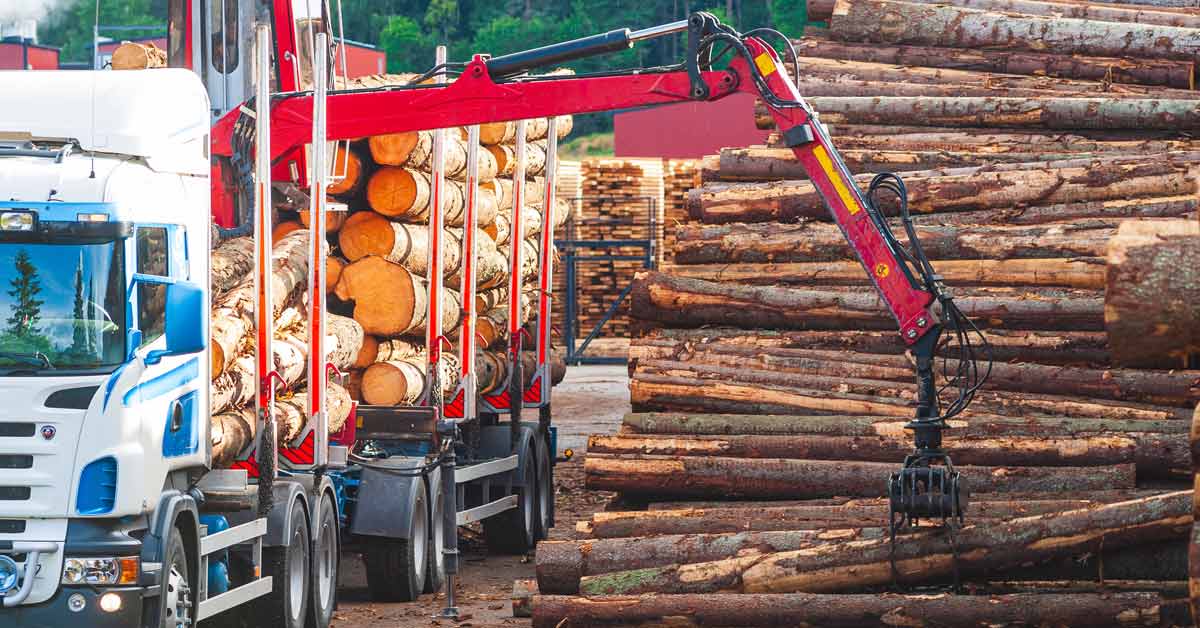
US–Canada Lumber Dispute Intensifies with Massive Tariff Increase
