2 min read
Thermoplastics Take Flight: Boeing and Airbus Look to Lightweight Composites for Next-Gen Jets
ResourceWise
:
Apr 2, 2025 2:59:31 PM
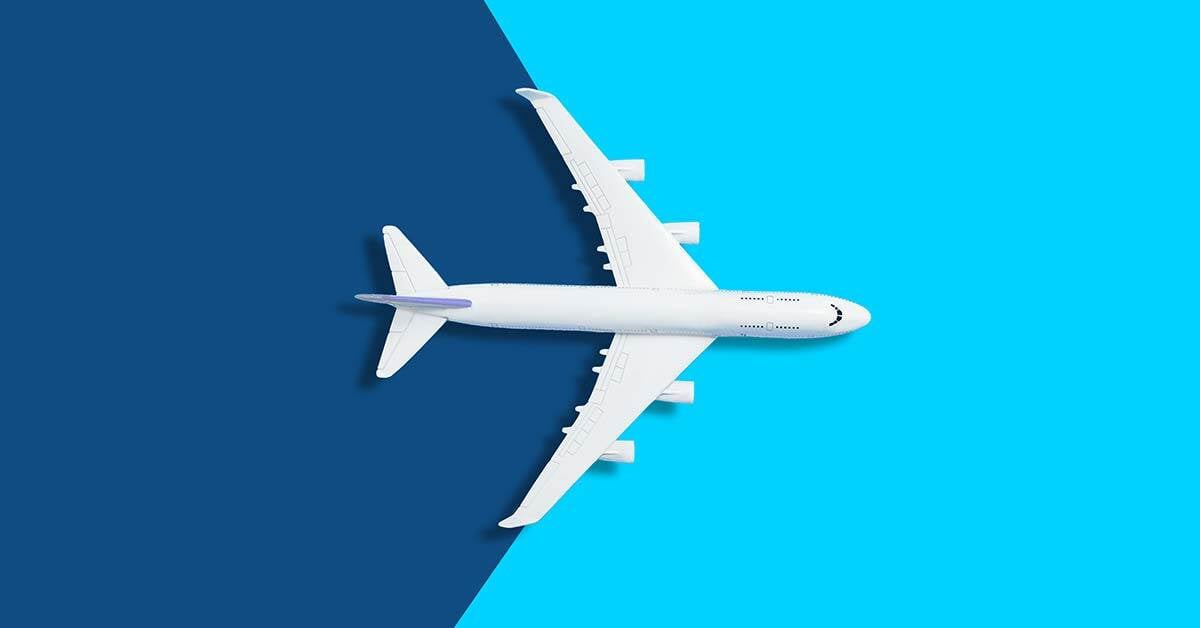
As the aerospace industry braces for a new era of high-speed production and sustainability, Airbus and Boeing are setting their sights on a transformative shift in aircraft manufacturing. Recent insights from industry sources reveal that the two giants are exploring thermoplastic composites to ramp up output for their next-generation jets, potentially reaching an ambitious 100 aircraft per month each. This pivot signals a growing demand for advanced materials and innovative production techniques for businesses in the chemicals supply chain—a trend worth watching closely.
A Push for Speed and Scale
The aerospace sector is no stranger to composites, with materials like carbon fiber already starring in widebody jets such as the Boeing 787 and Airbus A350. However, the focus is now shifting toward narrow-body workhorses—the Boeing 737 and Airbus A320 series successors—where traditional methods have historically constrained production rates. According to Reuters, both companies are eyeing thermoplastic composites to achieve production targets that dwarf current capabilities, with studies suggesting a baseline of 80 jets per month and aspirations stretching to 100.
This leap in output isn't just about volume; it's about efficiency. Thermoplastics offer a compelling edge over conventional thermoset composites and aluminum thanks to their ability to be reheated, reshaped, and welded using techniques like ultrasonic welding. Unlike thermosets, which require lengthy autoclave curing, thermoplastics promise faster assembly, reduced energy use, and lighter structures—key factors as Airbus and Boeing aim to meet rising global demand while addressing supply chain bottlenecks.
Why Thermoplastics Matter
The appeal of thermoplastics lies in their versatility and performance. As highlighted by Aerospace Tech Hub, these materials enable "ultrasonic welding" and eliminate the need for time-intensive curing processes, making them ideal for high-rate production lines. Engineers note that thermoplastics can reduce aircraft weight by cutting reliance on metal fasteners like rivets, which aligns with the industry's push for fuel efficiency and lower emissions.
Interesting Engineering underscores another advantage: thermoplastics' adaptability. Unlike aluminum, which has dominated narrow-body jets for decades, thermoplastics can be molded into seamless, aerodynamic shapes, enhancing performance and production speed. Boeing's participation in NASA's HiCAM program further signals a commitment to mastering these materials, with potential applications extending beyond aerospace into other high-performance sectors.
Challenges Ahead
The transition isn't without hurdles. Scaling thermoplastic use to unprecedented rates—potentially one 200-seat jet every few hours—requires a robust supply chain capable of delivering consistent quality at volume.
"Analysts say production capacity will be as important a battleground in tomorrow's jet industry as picking the right designs, as the West faces rising competition from China."
— "Exclusive: Airbus, Boeing eye fast output as plastics loom for future jets," Reuters
Regulatory hurdles, particularly around welding structural components, could also slow adoption. While thermoplastics promise recyclability advantages over thermosets, the infrastructure to support large-scale reuse remains underdeveloped.
For now, Airbus and Boeing are in research mode, with no immediate plans to replace their current flagships. However, their collaboration with consortia like Clean Sky 2 and NASA's HiCAM program suggests a serious long-term bet on thermoplastics—a bet that could reshape the competitive landscape as China's COMAC gains ground with its own offerings.