Raw material inventory management—the process that ensures a sufficient raw material supply to sustain production goals—involves a certain degree of risk management. Procurement organizations must strike a delicate balance between having enough woodyard inventory and minimizing holding costs. How much risk should a mill be willing to incur?
To properly assess risk, mills look at their product sales, translate that into a mill run rate and then factor in the available raw material supply. Deliveries are calculated based on historical trends and projected forward.
Delivery Plan = Planned Inventory – Current Inventory + Consumption
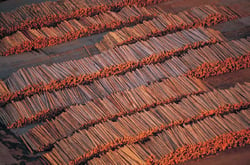
When all things are stable, this formula is fairly straightforward. Variability in the process, whether due toweather, seasonality, freight capacities and mill operating rates, complicates the equation, however. Variability is truly the enemy of the delivery plan. In general, higher variability means that price volatility increases and spot market purchases occur.
One example of this occurred in West-South pine pulpwood markets in 2010. Record-breaking rainfall in 2009 restricted harvest activity and mill inventories were drained as a result. Prices escalated at the end of 2009 and into 2010 as mills struggled to bring their inventories back into alignment with their production needs.
Because Forest2Market collects more than 30 million transactions of wood raw materials in its databases annually, we have become adept at predicting a significant portion of the variability in raw material procurement. Our long-term historical data is very good at helping show the variation in market inventories.
This data provides some insight into the risk tolerance of mills in the South. The month-by-month trend line, for instance, shows that over the last three years, total fiber inventory increased by six days southwide. This is an interesting development since no significant weather event occurred during this time frame and seasonal variation in the South is muted relative to other regions of North America. This increase in inventory suggests mills are less risk tolerant that they once were. (Click image to expand)
As inventory days increased, so did price. Our data shows that fiber price is approximately $3.00 per ton higher across the South since 2012, though this is not due to significant supply chain disruptions. Rather the price increase has been a fairly steady climb due to increasing competition and better economic conditions.
While individual mills may have experienced low inventory that resulted in the need for spot market purchases, the supply chain in the South has been fairly consistent since 2012. Inventories have generally averaged between 15 and 25 days with no significant price shocks in the supply chain. Measuring your individual mill’s inventory versus the market can be enlightening when planning annual budgets and monthly deliveries.
Conventional wisdom argues that holding lower inventory to save inventory cost is preferred as long as you don’t run out of wood. However, the real cost of holding lower inventory should include the expense of higher prices in the following quarter that can erode any cost savings realized as a result of holding lower inventory. These higher costs should be included in delivery plan risk assessments.
Particularly with today’s low interest rates, the cost savings of lower inventory don’t always compensate for the spot market purchasing that occurs when variability hits the supply chain. While we can never totally defeat the variability enemy in our procurement planning, we can reduce its impact by planning proper inventory levels that reflect historical deliveries and future challenges.