3 min read
Wood Fiber Supply Chain Characteristics Part 1: The Dollar’s in the Details
Pete Coutu
:
October 23, 2015
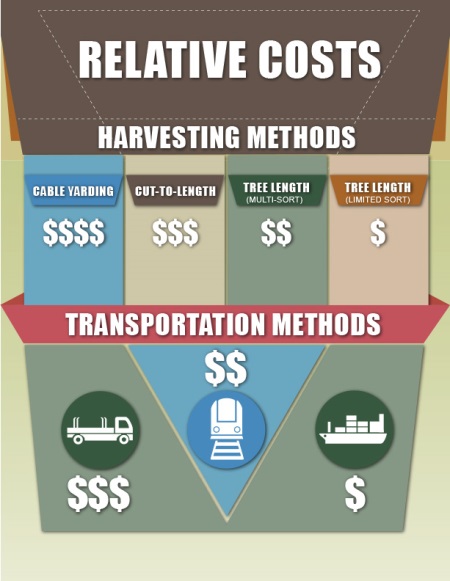
This is the first installment of what will be a two-part series on identifying opportunities for supply chain improvements within the forest products industry. The material is taken from a recent presentation I delivered at the Forest Resource Association (FRA) Lake States annual fall meeting in October.
During a recent FRA event in Wisconsin, I was asked to speak about wood fiber supply chain characteristics that are unique to different wood basins within the US, as well as other parts of the world that have healthy forest products industries. As I was doing research and pulling together the specifics for my presentation, I found it helpful to start the process with a wide-ranging view of each of these regions while asking a very simple question—one that is at the foundation of the forest products industry: What is the most efficient way to move wood raw materials from the stump to the mill?
It’s really quite a simple task when you think about it; moving a product from point A to point B is not a difficult concept. But when you begin to add a number of variables to the task, it becomes an increasingly complex undertaking. In the forest products industry, these variables include terrain, climate, changing regulations, infrastructure, proximity to the final destination and equipment demands, just to name a few. These variables dictate everything that occurs between point A and point B, creating an environment that demands flexibility. More importantly, these variables demand persistent attention to detail to remain successful and profitable.
The process of timber harvesting is essentially the same regardless of the wood basin. Timber is cut, moved or “skidded” to a landing site, loaded on a transportation vessel, and delivered to a destination where it will be merchandised and/or utilized. But the variables within each unique wood basin carry relative costs that can greatly impact the final or “delivered” cost of harvested timber. To build a framework for analyzing some of these relative costs by region, I categorized the essential functions within the supply chain: harvest type (primary and secondary) and transportation type. I then assigned generalized costs (from highest to lowest) to each of these functions based on some of the static variables in each region (note the infographic below). Also, keep in mind that these costs do not include stumpage or contracted wood fiber costs.
An analysis of the trends in harvesting and transportation told a story of efficiency and ingenuity that is unique to different wood basins and their terrains, climates and infrastructures. Regardless of the equipment used at any given harvesting site, the removal methodology fits the terrain; wood harvesting teams are resourceful, and when they’re working in a timber stand, time is money .
Some of the interesting regional trends include:
US South
-
Primary Harvest Type: tree length (limited sort)
-
Transportation: tree length hauling
US Great Lakes
-
Primary Harvest Type: cut-to-length
-
Secondary Harvest Type: tree length (multi-sort)
-
Transportation: truck with loader
US Northeast
-
Primary Harvest Type: tree length (multi-sort)
-
Transportation: random length hauling
Brazil
-
Primary Harvest Type: tree length (limited sort)
-
Secondary Harvest Type: cut-to-length
-
Transportation: long length hauling
Scandinavia
-
Primary Harvest Type: cut-to-length
-
Transportation: trucks with loaders
When applying the relative costs illustrated in the infographic to the individual regions, it’s safe to assume that, generally speaking, wood and fiber supply chain costs are lower in the US South primarily due to the static variables discussed earlier; the climate, terrain, harvesting seasons and equipment used in this region are vastly different from other regions. But what about some of the finer points that may not be so evident? Are there methods for uncovering some of the minutiae? Within each region, are there ways to trim costs that boost profitability?
The Dollar’s in the Details
Most large forest products companies are no longer vertically integrated, meaning they no longer own or manage the supply chain from the seedling to the processing facility. This is a trend that has become commonplace in just the last 10-15 years. As these companies have divested themselves of timberlands and, by proxy, the management costs associated with them, they have forfeited many of the benefits that come with access to on-demand wood fiber. While this aspect of the forest products industry has changed so dramatically in such a short timeframe, effectively managing the supply chain is more important now than ever before.
After analyzing the relative costs in the regional framework discussed above, I then used Forest2Market’s data to drill down another level within the transportation method category by analyzing average regional payload and haul distances. The results tell a different story, oftentimes highlighting regions that are advantaged due to the transportation infrastructure and proximity to a destination. Consider some of the data out of these regions:
While the high-level view of Brazil’s preferred harvesting and transportation methods did not appear to be as cost effective as the US South, its average payload is 32% higher and its average haul distance is 10% shorter. Likewise, note that the US Northeast averages the highest payload, but those savings may be erased due to the associated costs with long haul distances, which are nearly twice the average distances of Brazil.
The above case illustrates the importance of using quality data when analyzing wood procurement costs; high-level views are integral to making operating decisions, but they don’t always tell the whole story. In the next installment I will continue to drill down the data even further, uncovering individual supply chain pain points and identifying cost-saving opportunities along the way to boost the bottom line.
%MCEPASTEBIN%