6 min read
Stora Enso's Mill Closures Raise Questions for Uncoated Woodfree Producers
Matt Elhardt & Marko Summanen
:
August 3, 2021
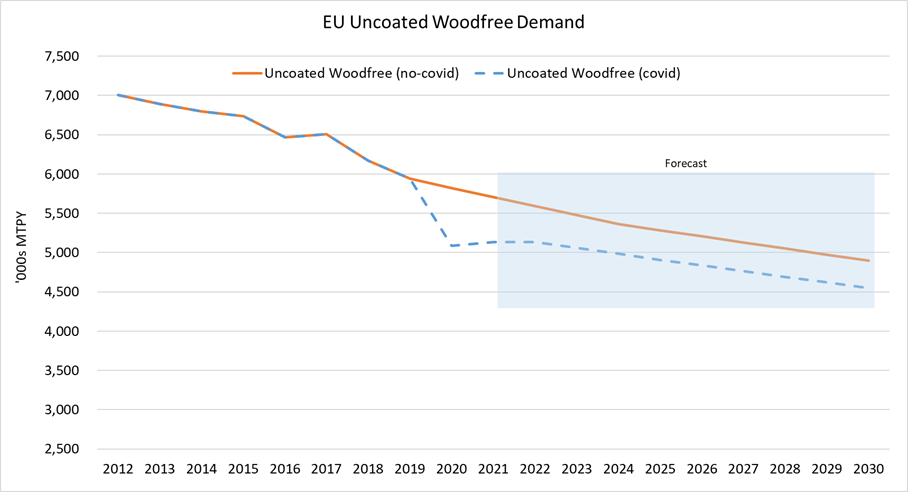
The ground continues to shift across the Europe as demand patterns in the uncoated woodfree segment have driven manufacturers to make some difficult decisions. Most recently, Stora Enso announced the permanent closure of two facilities operating in the uncoated woodfree, mechanical grades and newsprint segments in Kemi, Finland and Borlänge, Sweden. Pulp and paper production at the two facilities is scheduled to cease in 3Q2021.
The planned closures will reduce Stora Enso’s paper production capacity by 35% to 2.6 million tonnes per year (tpy) and come at a time when EU manufacturers are forced to match capacity to the declining demand trends that have accelerated during the COVID-19 pandemic.
Per the FisherSolve business intelligence platform, the Veitsiluoto mill in Kemi, Finland has a total capacity of 732,420 MTPY via three paper machines; two machines produce uncoated woodfree papers for office use and one machine produces coated paper grades for other print and packaging applications. Additionally, the mill has an integrated chemical pulp mill (414,000 ADMTPY), groundwood mill and a sheeting plant, as well as a functional sawmill. The planned closure of the site will impact all business segments aside from the sawmill, which will continue operations.
The Kvarnsveden mill in Borlänge, Sweden has two paper machines with a total capacity of 550,000 MTPY of supercalendered (SC) magazine papers and improved newsprint. The mill also has an integrated softwood thermomechanical pulp (TMP) line with a total capacity of 368,340 ADMTPY.
What impacts will this reduction in capacity have across the region?
We have witnessed a global shift in copy paper consumption develop over the last 20 years as widespread access to the internet has ushered in a new digital age—a profound change in accessibility, information gathering and knowledge sharing that is still developing at an ever-quickening pace. As a result, demand for printing and writing papers continues to decline as the digital age matures. However, the closure of offices and schools across the globe during the COVID-induced lockdowns has driven an accelerated demand destruction of this segment. As an example, our models estimate that workers use only 25% of the copy paper when working from home then they do at the office.
Source: European Association of Graphic Paper Producers, 2021
Despite the large gap that now currently exists between uncoated woodfree demand and production capacity in Europe, this grade was relatively healthy before the pandemic. European export volumes and prices were very strong in 2018, which was driven by robust demand from North Africa, North America and the Middle East. However, with Europe capacity now declining in a post-pandemic economy, together with increased pulp prices, exports are likely to taper in the short run.
Source: FisherSolveTM Next 2021 Fisher International, Inc.
Though Stora Enso’s recent move seems reactionary on the surface, the data suggest that further capacity reductions are still needed to better match updated demand patterns to production capacity.
Total uncoated woodfree capacity across Europe in 1Q2021 was approximately 9.5 mMTPY. While Stora will continue producing uncoated woodfree papers at its Nymölla mill in southern Sweden, the Veitsiluoto closure will result in a capacity reduction in the EU of more than 9.5% to 8.7 MMTPY. Prior to Stora’s announcement, the European uncoated woodfree market was fragmented with no one producer commanding a majority share and Stora owning 10% of the total capacity.
European Uncoated Woodfree Capacity Shares 1Q2021 (Before Stora Enso Closures – 2Q2021)
(Shares less than 3% in “All Other” category)
What mills are at risk during this transition?
While this development raises a number of questions, we can use business data and models to define likely scenarios moving forward. Production costs, asset health, logistics and profitability concerns will define “next steps” for manufacturers who commit to the changing dynamics of this segment. Should pandemic-related restrictions ease enough to allow a slow reopening across Europe, there will at least be a short-term increase in demand as businesses and schools resume previous patterns. That said, producers expecting a widespread return to pre-2019 activity will be disappointed.
Cost benchmarking is an accurate tool to help manufacturers better understand their competitive positions as demand patterns shift. However, in the current uncoated woodfree market across the Europe, cost benchmarking doesn’t provide a full-spectrum view for maximizing strategic decision making; producers need to understand all the factors predictive of longer-term asset performance. Viability Benchmarking, a FisherSolve tool, can be used to assess the overall risk of a mill (its likelihood of closing). The model takes into consideration factors that over time have proven to be predictive of a mill closing, like technical age, scale, costs, capital costs, among others. Over time, it has proven to be an accurate tool to predict eventual machine closures.
Assuming that small mills / companies will likely have no choice but to “fight as long as they can”, let’s use viability to evaluate the top 5 WFU producers and their mills. What can modeling tell us about manufacturer competitiveness? Using benchmark viability, we can see that Stora’s mills are on the high side of risk when compared with their peers making the same grades in Europe. It’s no surprise then, that SE made the announcement they did.
Source: FisherSolveTM Next 2021 Fisher International, Inc.
The cost benchmarking curve below (which includes all European producers) suggests that profitable production also requires access to low-cost kraft pulp. As can be seen from the chart, non-integrated mills (that is, those that buy market pulp to make paper) are on the right side of the cost curve. In the current inflationary environment of rising pulp prices, these mills will face even more pressures on margins, particularly if the low-cost mills choose to use their integrated cost advantage to gain market share.
Uncoated Woodfree Mills – Europe 1Q2021
Mfg. Cash Cost/MT (FOB Antwerp)
We can also get an idea of which way the arrow is pointing by considering who will likely absorb the production gap resulting from Stora’s exit from the uncoated woodfree market. Classic economic theory tells us that over time, mature industries in declining segments consolidate as weaker producers exit. Work we have done, together with our partner STE Analytics, Oy, tells us that these periods of consolidation can often be painful – right up to the point when a market stabilizes, at which point survivors enjoy lower costs and more stable margins.
Will there be enough consolidation in the segment to reach this level? On one hand, producers with a 4th quartile cost structure will maintain the floor price in soft market conditions and during these times, the floor price creates a guaranteed margin for low-cost producers. On the other hand, consolidation that might result in more stable margins through economies of scale vis-a-vis competitors requires growth in share. In segments with declining demand, this requires that strong mills “outlast” the week ones, which lowers the long-run economic clearing price, and possibly margins (a phenomenon we have witnessed in market pulp). Consolidation via the “last man standing” approach can be an expensive strategy if turning points are not well understood, along with the production costs of competitors.
IP’s recent announcement to divest its WFU business globally into a new company, as well as sell its Kwidzyn mill in Poland, should provide clues into the company’s own speculation about the segment. What will happen to IP’s Svetogorsk mill in Russia? Will it be sold to the joint venture Ilim Group? What does the future hold for IP’s Saillat Sur-Vienne mill in France? Can it possibly be integrated for kraft pulp production? The biggest question now: How will the other players respond over the next few years?
What Might the Future Look Like?
What are the options for European producers who simply aren’t competitive? Some of these mills can convert their machines into other grades. This becomes an easier transition if they are already operating in target segments elsewhere in their business, e.g., moving into a containerboard grade can be more costly for a mill that does not also own downstream corrugating.
However, some machines are not suitable for new grades due to their size, speeds, configuration etc. For example, Stora Enso’s current machines are likely too big to take advantage of the specialty growth grades that are replacing plastic in food packaging and in other plastic substitution products. However, some of the smaller machines can be a perfect fit for a such conversion, especially if there is kraft pulp on site and coating equipment in the machines.
Converting the Veitsiluoto and Kvarnsveden machines to produce containerboard may not be a feasible idea for Stora Enso at this point. Theoretically, Veitsiluoto could convert its machines for market pulp, although the long-term success of such a move would require larger volumes and significant investment in fiber production assets, which may not return the cost of capital, given the cyclicality of market pulp and the longer-term trends of falling cross-cycle real prices due to mega-pulp investments in other regions with comparative advantage.
Key questions major players need to be asking in the wake of Stora’s announcement:
- Will this change make it more difficult for producers to service Europe cost effectively?
- Will exports decrease as a natural reaction to capacity adjustments? Will this benefit producers in other regions an if so, which producers will benefit?
- Who will be the “last men standing?” Which large, EU producers will consolidate WFU market share as competitors decide to exit the category?
- Will there be enough consolidation to encourage the surviving companies to invest in the future?
- Russian producers have a real cost advantage in this segment. The drop in Russian demand has not been as severe as the EU, which provides them an advantage in this segment. Can Russian producers capture market share as EU producers drop off?