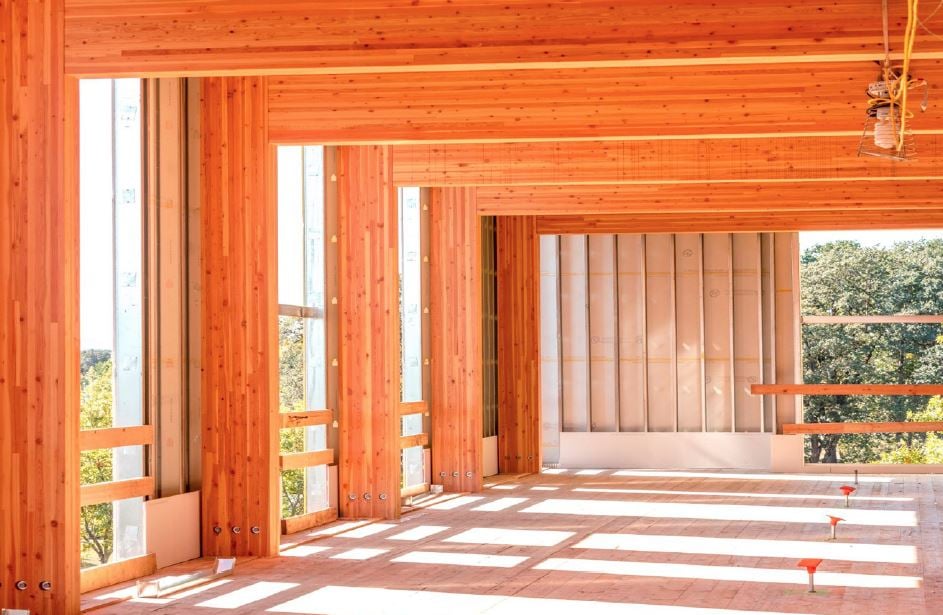
Per a recent addendum to Oregon’s building code, Portland continues to be a source for visionary timber innovation and construction projects. Oregon is now the first state in the country to allow timber buildings that are higher than six stories to be constructed without special allowances. However, new building classifications were introduced to alleviate any confusion.
The allowance was made possible when the International Code Council (ICC)—a non-profit upon which Oregon models its building codes—established a 2015 ad hoc committee on tall wood buildings to explore the benefits and challenges of mass timber and cross-laminated timber (CLT) building products. Earlier this year, the committee’s suggestions for these products were adopted that introduced standards and best practices for fireproofing, load-bearing potential, water resistance, sealing, seismic ratings and other criteria.
As a result, three new building classifications were introduced in Oregon via the new addendum:
- Type IV A - timber buildings permitted up to 18 stories and 270 feet tall at a maximum
- Type IV B - timber buildings permitted up to 12 stories and 180 feet tall at a maximum
- Type IV C - timber buildings permitted up to 9 stories and 85 feet tall at a maximum
Type IV C structures are allowed to use exposed timber as an interior finish, however Type IV A structures must enclose all exposed surfaces and include a three-hour fire-resistance rating for the structural elements.
“We congratulate the State of Oregon on becoming the first state to provide building code recognition for construction of tall, mass timber buildings,” said American Wood Council President & CEO Robert Glowinski in a statement. “Mass timber is a new category of wood products that will revolutionize how America builds and we’ve seen interest in it continue to grow over the last several years. This action by the Codes Division Administrator helps code officials in Oregon by making provisions consistent throughout the state. In adopting this new method, Oregon has also recognized the significant environmental benefits that accrue from greater wood product use.”
Building the Future with Wood
As we’ve reported in recent months, CLT and mass timber are increasing in popularity on global basis as reliable and affordable construction materials. The eight-story Carbon12 project in Portland recently became the US’s tallest timber building, and mass timber was deemed to be the most suitable material for First Tech Federal Credit Union’s new campus in Hillsboro, Oregon, which was covered in a new case study by The APA – The Engineered Wood Association. The design for the five-story, 156,000-square foot building was the product of a collaboration between First Tech, Hacker Architects, Kramer Gehlen & Associates engineering and general contractor Swinerton Builders.
The team evaluated available material options during the design phase of the project, and wood was the winner. “We allowed steel to compete with mass timber throughout the evaluation,” said William Silva of Swinerton. “From time to erect, fireproofing, foundation systems, and other criteria, wood came out on top every time.”
Interior of new First Tech Federal Credit Union campus. SOURCE: APA. PHOTO CREDIT: Mike Brewington for Swinerton Builders
Exterior of new First Tech Federal Credit Union campus. SOURCE: APA. PHOTO CREDIT: Mike Brewington for Swinerton Builders
Because mass timber panels are prefabricated, smaller crews can assemble structures more safely and in less time. The speed advantage is amplified because manufacturing can occur simultaneously with site and foundation work, reducing down time between construction phases and shortening construction time.
Highlights from the First Tech project include:
- The use of CLT and glued-laminated beams provided a 4 percent cost savings and reduced construction by four months.
- The First Tech building sequestered an estimated 4,621 tons of carbon and avoided 1,788 tons of greenhouse gases that would have been emitted through steel manufacturing and construction.
- Pre-planning and offsite hole-drilling resulted in faster and safer onsite construction with less disruption to the surrounding neighborhood. All the components were delivered to site as prefabricated pieces that were ready for assembly.
As promising as these building materials are, it’s important to note that they have also faced their share of challenges in the market—as do all innovative materials.
- Construction at a three-story, 80,000-square-foot building slated to become the new home of Oregon State University’s College of Forestry was halted earlier this year after a CLT panel collapsed. Engineers have since determined that least 85 of the panels will need to be replaced, putting the Corvallis building a year behind schedule and nearly $20 million over budget.
- In Portland, developers recently put the 12-story Framework building on hiatus due to high construction costs. A project representative said “The postponement is a result of changing market conditions over the past two years including inflation, escalating construction costs, and fluctuations in the tax credit market." It would have been the tallest CLT building in the country.
Despite the setbacks, a number of CLT-related projects are still forging ahead in the region. Portland-based Beam Development broke ground earlier this summer on a six-story, 110,000-square foot office building, The Nature Conservancy plans to include CLT panels in an addition to its Portland headquarters and Clackamas County is considering using the technology in its new courthouse.
One of CLT’s earliest adopters and proponents in North America, Michael Green Architecture, also continues to have a "large number of clients interested in CLT.” Green says his firm currently has 14 wood projects in various stages around the globe.
Beam Development principal Jonathan Malsin touched on a subject that really highlights the appeal of these wood-based materials. In our ever-quickening global economy, there is an increasing desire for locally-sourced products, and CLT provides a “local” experience while supporting the regional economy. "It's pretty exciting to be able to source a product that is fabricated here. It's driving a unique and virtuous connection between the urban and rural worlds in Oregon."