2 min read
Next-Generation Sawmills Must Master Supply Chain Efficiencies
Bryan Beck
:
March 11, 2019
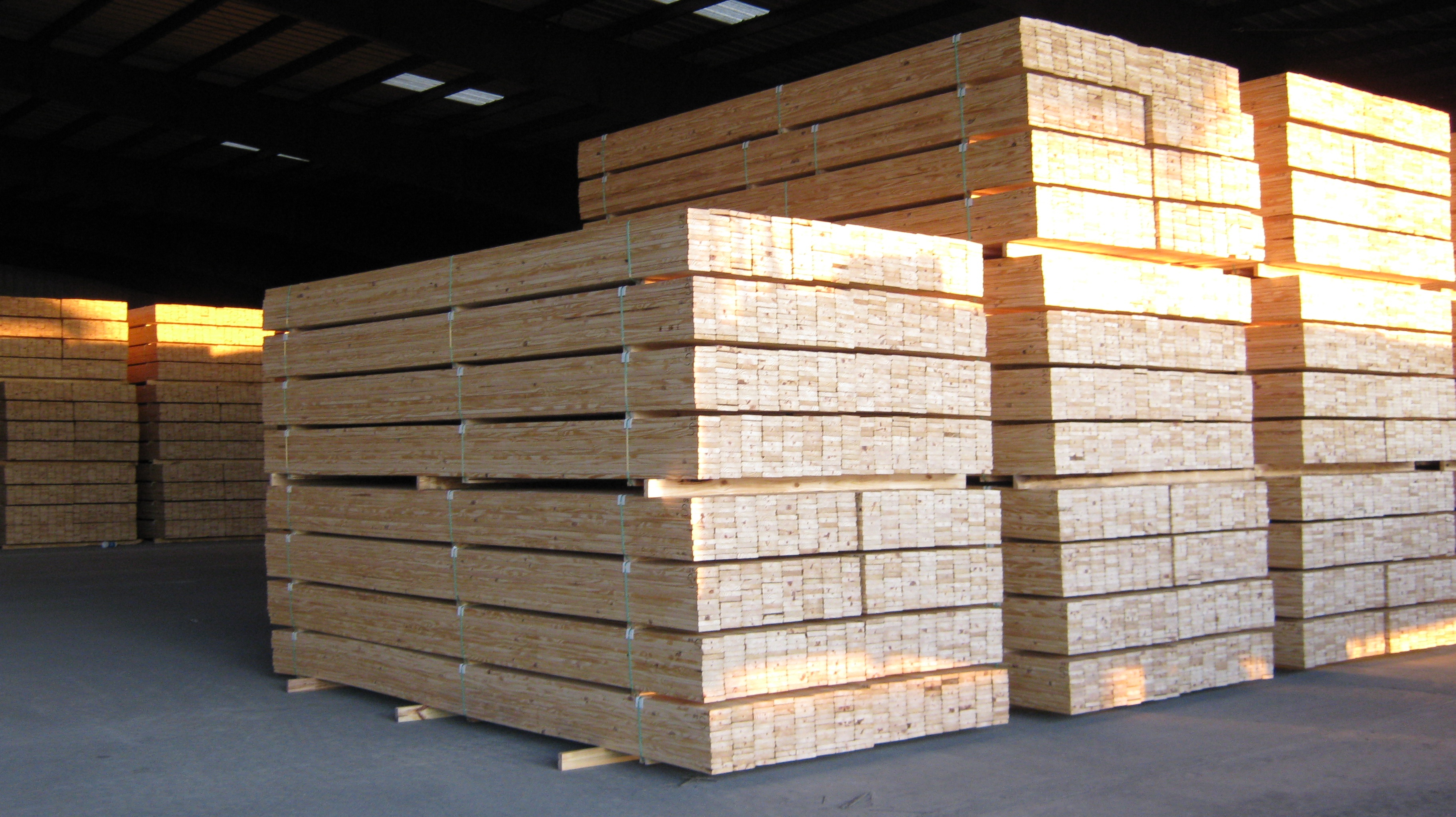
The forest products supply chain is a complex system of resources, organizations, activities, people, information, technology and market conditions—all of which must interact to move a product from a supplier to a customer. Efficient and well-managed supply chains are critical in the US South’s sawmill industry because log costs represent the single largest operating cost and, unlike the sawmill industry in other parts of North America, average log inventories at southern yellow pine (SYP) sawmills are very low.
According to Beck Group benchmarking data, southern mills keep an average of about 6 days of log inventory on hand compared to an average of nearly 40 days of log inventory among mills in the Western US. Any upset in the SYP supply chain can quickly affect sawmill operations.
How do SYP sawmill procurement managers manage supply chain efficiencies?
Centralized Purchasing Programs – over the last decade the ownership of the SYP industry has changed dramatically. Historically, the industry was characterized by many independent and family-owned operations with each making their own log purchasing decisions. Under those conditions, the various operations were likely making decisions and taking actions very differently than those of other operations in the industry.
Today, after a 10-year acquisition spree, there are five companies who (combined) own more than 70 mills and control over 60 percent of the lumber production capacity. In this situation, those large companies can implement a coordinated log purchasing program across their broad procurement region. The result can increase the efficiency of: logging and hauling operations; allocation of logs to specific mills; and mitigate volatility in stumpage and delivered log prices.
Evolution of Log Market Information – there is a long history of published log prices that mill procurement can use to help guide purchasing decisions. However, in recent years the march of technology has entered this arena too. For example, rather than relying on a survey to take a sample of log prices, Forest2Market has established a stumpage and delivered log cost price benchmarking reporting service. The prices reported are based on millions of transactions collected directly from subscriber’s financial records.
This approach creates a richer and more accurate database of log market conditions than log price reporting based on a much lower intensity sample. Additionally, Forest2Market recently developed SilvaStat360, a web based information portal that puts log market information at subscriber’s fingertips on a 24/7/365 basis.
Use of Middlemen – another difference between the US South and other North American regions is that in the South there is a significantly greater proportion of small, private landowners than in other regions where timberland is more likely to be owned in large blocks by industry or state and government agencies. This means that log procurement has evolved with heavy use of “Dealers” who are essentially middlemen that consolidate logs from multiple small private owners into larger volumes for more efficient, higher volume transactions with mills.
Sawmill TQ - the next step in the evolution is the development of Sawmill TQ, a partnership between The Beck Group and Forest2Market where SYP sawmill performance including key metrics such as manufacturing cost, productivity, staffing, yields, product mix, and log costs are all benchmarked and delivered via the SilvaStat360 portal. The fresh, accurate, and representative mill operation data delivered by this new tool will further help SYP mills drive efficiency in their supply chains.