3 min read
How Southern Lumber Manufacturers Succeed Despite Volatility
Joe Clark
:
November 12, 2020
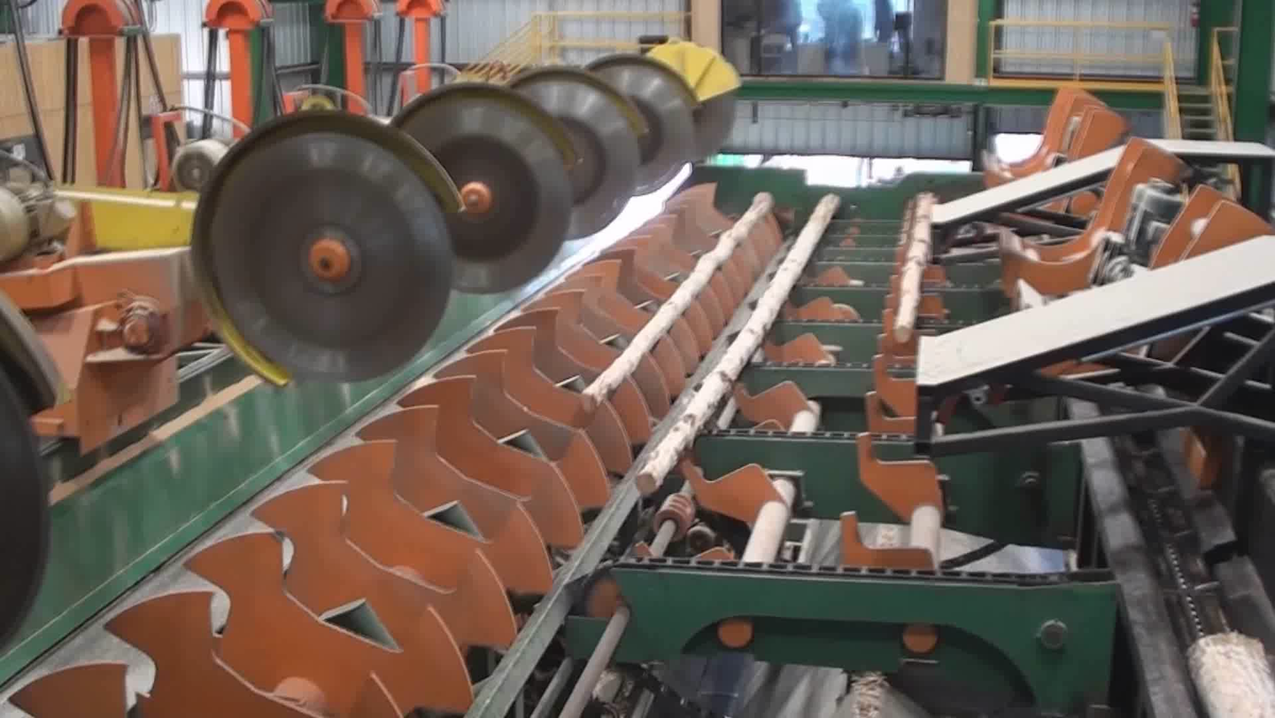
The North American lumber sector has been front-page news for the past several months, as sky-high prices for finished lumber products have markedly impacted new housing costs. Prices for southern yellow pine (SYP) lumber peaked in September and set new records by huge margins. But like many other volatile commodities markets, prices corrected course and tumbled even more quickly than they ascended; since peaking at $928 per thousand board feet (MBF) in September, SYP prices have now dropped 50 percent.
The lumber price run-up has caught the attention of a number of forest products manufacturers across the globe who have been eyeing the US South as a reliable, low-cost destination. Efficient and well-managed supply chains are critical for US South sawmillers because log costs represent the single largest operating cost, but things haven’t always been so rosy.
Recent History
In 2012, things were pretty good for most southern yellow pine sawmills. Those that survived the US housing crisis and the Great Recession (the South lost 39 lumber/OSB mills from 2007-2017) were making decent profits for the first time in years, most had their pick of the oversupplied timber market, and the future looked bright. In that same year, the average mill was producing about 125 million board feet (MMBF) and they were doing it in only about 60 hours per week, which was more volume than they had produced before, and in fewer hours.
Many of these mills were bumping up against kiln drying constraints and couldn’t produce more lumber even if they were to run the standard 80-hour week. At that time, only a few mills in the US South were capable of producing more than 200 MMBF in a year.
Fast forward just a few years and the southern lumber landscape began to change dramatically. A number of new sawmills were constructed and came online across the region—some of them boasting annual capacities of 250 to 300 MMBF. Existing mills have also aggressively expanded by adding drying capacity, running longer hours and upgrading equipment to take advantage of the plentiful SYP timber resource.
Today, after a 10-year acquisition spree, there are five companies who (combined) own more than 70 mills and control over 60 percent of the regional lumber production capacity. In this situation, those large companies have incredible influence and flexibility within the market. For instance, they can implement a coordinated log purchasing program across their broad procurement regions that can increase the efficiency of logging and hauling operations, increase the allocation of logs to specific mills, and can mitigate volatility in stumpage and delivered log prices.
The Beck Group projects that the average SYP sawmill production levels will rise from 125 MMBF in 2012 to over 200 MMBF a decade later. How does this compare to other regions? The following chart illustrates the relative scale of sawmill operations in key production areas of North America.
As the chart indicates, southern yellow pine mills rival production levels of their counterparts in the US Coastal West region. However, large scale mills in the British Columbia (BC) Interior will continue to hold the top ranking for annual production per mill, though they are likely to face increasing fiber supply pressures in the coming years.
How do southern sawmillers manage supply chain efficiencies and maintain profitability in the unpredictable circumstances we have been navigating for the last several months?
- Log Accessibility & Inventory Management - according to Beck Group benchmarking data, southern mills keep an average of about 6 days of log inventory on hand compared to an average of nearly 40 days of log inventory among mills in the Western US. Any upset in the SYP supply chain, however, can quickly affect sawmill operations.
- Centralized Purchasing Programs – over the last decade the ownership of the SYP industry has changed dramatically. Historically, the industry was characterized by many independent and family-owned operations with each making their own log purchasing decisions. Under those conditions, various companies were likely making decisions and taking actions very differently than their competitors.
- Evolution of Log Market Information – there is a long history of published log prices that mill procurement teams can use to help guide purchasing decisions. However, in recent years the application of data has entered this arena too. For example, rather than relying on a survey to take a sample of log prices, Forest2Market has established stumpage and delivered log price benchmarking reporting services. The prices reported are based on millions of transactions collected directly from subscriber’s financial records.
- Use of Middlemen – another difference between the US South and other North American regions is that the South is home to a significantly greater proportion of small, private landowners than in other regions where timberland is more likely to be owned in large blocks by industry or government agencies. This means that log procurement has evolved with a heavy reliance on “dealers” who are essentially middlemen who consolidate logs from multiple small private owners into larger volumes for more efficient, higher-volume transactions with mills.
- Sawmill TQ - the next step in maximizing sawmill profitability is Sawmill TQ, a partnership between The Beck Group and Forest2Market. Sawmill TQ provides a reliable benchmark for SYP sawmill performance that includes key metrics such as manufacturing cost, productivity, staffing, yields, product mix, log cost and profitability. The fresh, accurate and representative mill operation data delivered by this tool helps forward-looking SYP mills to drive efficiency in their supply chains—regardless of market turbulence.
The increase in average southern sawmill size will have significant impacts on productivity and manufacturing costs, delivered log costs, and other operating metrics in the coming years. With the rise of business intelligence like Sawmill TQ, lumber manufacturers are becoming more sophisticated in how they collect and share data. The most sophisticated mills will use the increasing abundance of information to make data-driven decisions to rapidly identify and respond to changing trends. Improved productivity, lumber recovery, superior grade yields and data-driven decision-making will allow these mills to maximize their productivity in a highly competitive environment.