2 min read
3Q2011 Containerboard Mill Activity – US South and Pacific Northwest
Suz-Anne Kinney
:
November 30, 2011
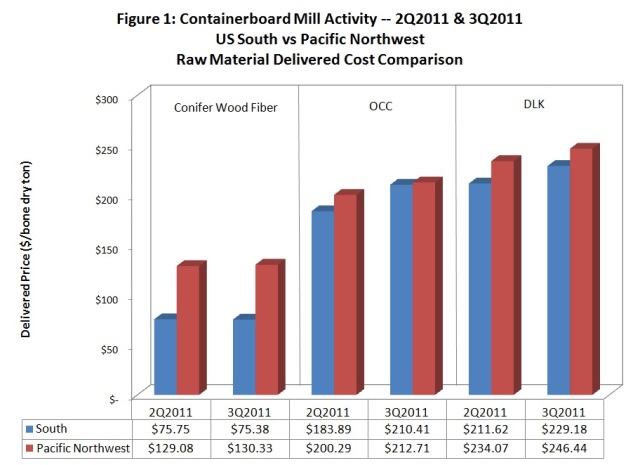
Containerboard mills in the US South and Pacific Northwest experienced increased raw material costs in 3Q2011. Figure 1 compares 3Q and 2Q prices for conifer wood fiber, OCC and DLK.
As Figure 1 shows, conifer wood fiber costs in the two regions moved in opposite directions during the quarter[1]. US South delivered prices were down 0.5% or $0.37 per bone dry ton (BDT) while Pacific Northwest prices were up $1.25 per BDT, a 1.0% increase. Supply of wood fiber was not an issue for southern mills as prices dropped despite a 3.7% increase in mills’ consumption volume. US South wood fiber prices were 58% ($75.38) of the cost of the Pacific Northwest average of $130.33 per BDT. Pacific Northwest consumption volume increased 11.3%.
For recycled fiber, delivered prices for old corrugated containers (OCC) increased in both regions. US South prices increased $26.52 per ton, or 14.4%. Southern mills were building inventories over the quarter, stepping up their consumption volume by 6.1%. In the Pacific Northwest, prices increased $12.42 per ton (6.2%) despite the fact that their consumption volume fell by 4.5%[2]. For 3Q2011, price differences between the regions shrank. In 2Q2011, southern delivered prices were 92% of the northwestern average of $200.29 per ton. For 3Q2011, southern delivered prices were more on par, averaging $210.41 per ton or 99% of the Pacific Northwest average.
For double-lined, kraft corrugated cuttings (DLK), US South prices increased by $17.56 per ton (8.3%). Consumption volume of DLK was higher by 1.9%. In the Pacific Northwest, prices increased $12.37 per ton (5.3%) while consumption volume contracted by more than 20%. In the third quarter, US South DLK prices were 93% of the cost of the Pacific Northwest average of $246.44 per ton, or $229.18 per ton.
Forest2Market collects pricing data for wood fiber (through its delivered raw material benchmark) and recovered fiber (through its Market2Mill recovered fiber benchmark). By combining these resources, we can take a more granular look at the mix of products being consumed by containerboard mills; Figure 2 combines wood fiber and recycled fiber into a composite raw material cost and provides insight into how mills are allocating consumption volume among raw materials to decrease their costs[3].
In the US South, the product mix for 3Q2011 containerboard production was approximately 73.1% virgin wood fiber, 22.1% OCC fiber, and 4.7% DLK fiber. Pacific Northwest mills used less wood fiber than mills in the South in the third quarter and more OCC; the product mix for northwestern containerboard production was approximately 60.9% wood fiber, 34.9% OCC fiber, and 4.3% DLK fiber.
Based on the composite delivered price, southern mills experienced a $6.15 per BDT increase in raw material costs (5.5%) to average $118.90 per ton in 3Q2011. This increase was alleviated somewhat by mills altering their fiber mix to use more virgin wood fiber, which was decreasing in cost, and less high cost OCC.
In the Pacific Northwest, the composite delivered price averaged $173.41 per ton in 3Q2011, an increase of $3.95 per ton (2.3%). Northwestern mills moved 2.1% of their product mix to virgin wood fiber, 1.2% away from OCC fiber and 0.8% away from DLK fiber (the discrepancy from Figure 2 is due to a rounding error).
Overall, the cost of containerboard production in the US South was just 69% of the cost of Pacific Northwest production. Still, costs in the South increased in 3Q; quarter over quarter, they gained 2% against Pacific Northwest pricing.