3 min read
Plastic Packaging Material That Is Both Sustainable and Biodegradable
Jane Denny
:
May 6, 2022 12:00:00 AM
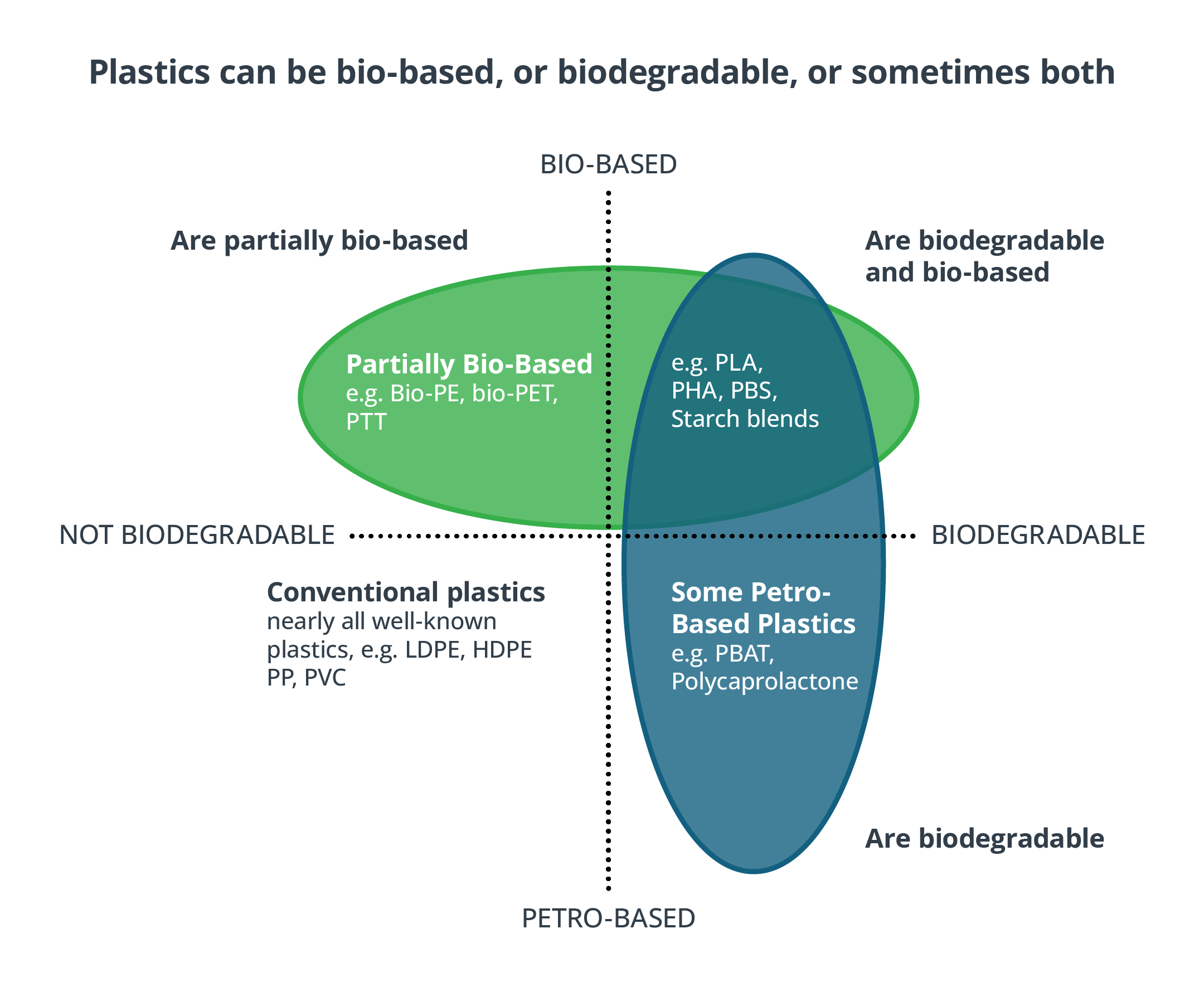
Ideally, plastic packaging should be both biodegradable and produced in a sustainable way, but this is rarely the case. Bio-PET is partially sustainable, but it is not biodegradable. PBAT is biodegradable but is made from petroleum-based feedstocks.
One material that is both is polyhydroxyalkanoate (PHA) and, in this respect, it has few rivals besides the equal propertied polylactic acid.
Natural PHAs are produced by an extensive variety of microorganisms through bacterial fermentation. Due to its high performance, biocompatibility, biodegradability, and green credentials, the PHA family has a large design space and accommodates a wide range of market applications, as a broad variety of different polymers can be produced and blended.
Source: The Fiber Year
Mimicking Nature – The PHA Industry Landscape Report 2022 – a new study from nova-Institute and PHA coalition GO!PHA – estimated installed PHA manufacturing capacity at under 50 ktpa as 2021 ended.
Changing Fortunes
The nova-Institute research team did however note ‘momentum for this new polymer platform...rapidly changing for the better’ and predicts that PHA manufacturing capacity will increase to 570 ktpa by 2027.
In the last 20 years, natural PHAs have been intensively researched and a number of industrial-scale plants have been built, though there have been some false starts along the way.
Next month, for example, will see the latest in a string of attempts to sell what is left of Italian PHA manufacturer Bio-on following bankruptcy. Its assets – including labs and warehouses, patent portfolio, and shareholdings – were once valued at over $100m but several sale attempts have so far failed.
On the Market
Japan’s Kaneka however, is a PHA-based polymer success story with its Green Planet branded product available at a capacity of 20ktpa from February 2022.
Source: Bacardi
US-based Danimer Scientific’s signature polymer Nodax uses canola oil as a primary feedstock. The company has partnered with Swiss food company Nestlé to develop biobased and biodegradable plastic bottles for the latter’s water business using Nodax. The move is part of Nestlé's vision to make its packaging recyclable or reusable with a particular focus on avoiding plastic waste. Between 2020 and 2025, Nestlé will phase out all plastics that are non-recyclable – or hard to recycle – for all its products worldwide.
Danimer is also collaborating with Bacardi on a new 100% biodegradable bottle for use across the spirits company's portfolio of brands from 2023. The drinks manufacturer wants to replace 80 million plastic bottles per year, equivalent to 3ktpa of plastic, with a biobased alternative. The bottle, which is based on Danimer’s Nodax PHA is expected to biodegrade in 18 months with no microplastic residues.
PHA resin technology from Danimer is used in the compostable bag of PepsiCo’s Frito-Lay – Off The Eaten Path – snack brand. In collaboration with PrintPack, Frito-Lay developed the product to include sound/dampening technology. The move was to avoid the unprecedentedly loud crinkling noise that saw earlier attempts at compostable packets – for SunChips brand snack – pulled from retail a decade ago.
Source: Frito-Lay
Pipeline PHA
PHA extraction technology owned by Bioextrax – a biotech firm based in Sweden – has given the go-ahead for a scaled-up evaluation project to an as yet undisclosed EU-based PHA producer. The latter has a 12-month window to validate the tech – a process that could trigger a commercial agreement for the use of Bioextract's process within its own commercial production and further licensing.
Bioextrax’s patent-pending PHA from sucrose conversion method is 100% biobased, chemical, and solvent-free and works with all PHA-producing bacteria and PHA types, the firm says. The technology leaves a nutrient-rich solubilized non-PHA bacterial biomass as a co-product (20-50% weight of cell biomass) and enables more than 50% cost reduction compared to other PHA-producing methods.
After: European Bioplastics
A thermoplastic resin suitable for injection molding, thermoforming, and extrusion, Enmat Y1000 PHBV from Chinese firm TianAn Biologic has been certified as biodegradable in seawater – and passed home composting testing – by Austria-based certification body TÜV.
Reportedly heat-resistant to 160ºC, it can be blended with biopolymers including PLA, starch-based polymers as well and synthetic biobased polyesters. The current output from TianAn Biologic’s Ningbo City facility is 2 ktpa.
Eco-Friendly Ambition
South Korea’s Lotte Chemical aims to commercialize a PHA-based bioplastic material it is developing in partnership with Chung-Ang University by 2023. The strategy complements its plans to invest $500 million in eco-friendly materials plants within a domestic petrochemical complex.
The moves coincide with the Ministry of Trade, Industry and Energy and the Ministry of Environment support for increased use of recycled materials and biobased plastics.
The target is to replace 15% of industrial plastic use and 20% of non-industrial use with alternative materials by 2030 – targets that will likely increase in succession by 45% and then 100% by 2050.
In April 2022, South Korea’s CJ CheilJedang shipped the first batches of its PHA-based material from its 5ktpa capacity facility in Pasuruan, Indonesia. As reported in Tecnon OrbiChem’s May 2021 BioMaterials & Intermediates ChemFocus, the company co-developed compounded PLA and PHA resins with chemical and film company SKC. Intended as products both would market, CJ CheilJedang earmarked the product for its Happy Bean Tofu wrapping.
Source: SKC
In its press release last week, CJ CheilJedang recognized that despite the product being a move in the right direction in terms of sustainability, ‘the issue of full biodegradability – particularly in marine and home environments – has yet to be addressed’.
The Future of Packaging
The remaining question over the biodegradability of their co-developed product distills much of the discussion around this relatively new packaging solution. For companies keen to explore the options around sustainable and eco-friendly packaging, GO!PHA and partner Netherlands-based biotech firm Helian Polymers provide PHA samples for academic, research, and development purposes at its PHA Sample Shop.
Consumers are turning their backs on packaging that may increase plastic waste in our oceans and environment. Moving forward, they will support brands demonstrating Environmental, Social, and (corporate) Governance principles that protect our world and future.