1 min read
Developing Renewable Polycarbonates: A Balancing Act
ResourceWise
:
Jul 29, 2021 12:00:00 AM
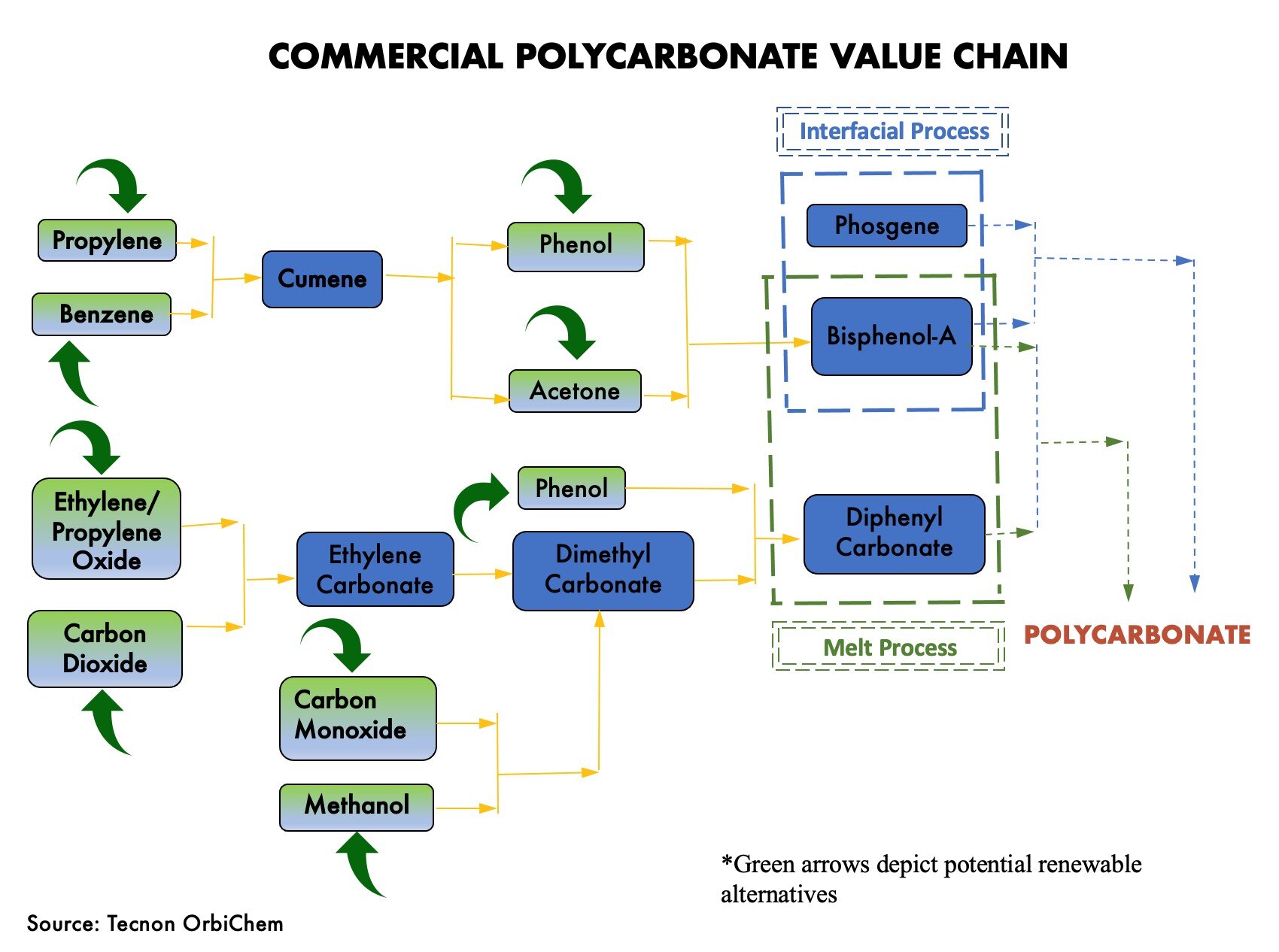
There are limited developments and commercialisation in the field of plant-based polycarbonates due to the complicated technical properties of the material, and it usually takes time to develop alternative chemical intermediates that can replace the key raw materials in producing polycarbonates without altering performance. Several traditional producers are using waste carbon feedstock or the mass balance approach to produce certified renewable polycarbonate using bio-based hydrocarbon feedstock.
Polycarbonates (PC) are an unusual and extremely useful class of high heat polymers known for their toughness and clarity. The polycarbonate most used is produced by condensation polymerisation between BPA and either carbonyl chloride (also known as phosgene) or diphenyl carbonate. However, an increasing proportion of polycarbonates is made via diphenyl carbonate, in order to eliminate the use of phosgene, an extremely poisonous gas. The development of phosgene free diphenyl carbonate (DPC) process which is also known as the melt process has the advantage of lower capital and feedstock costs. Asahi Kasei started their development of a non-phosgene aromatic PC production in 1977. Commercialisation of the process occurred in 2002 with the first plant located in Taiwan by the Chimei-Asahi Corp., a joint venture between Asahi and Chi Mei Corp.
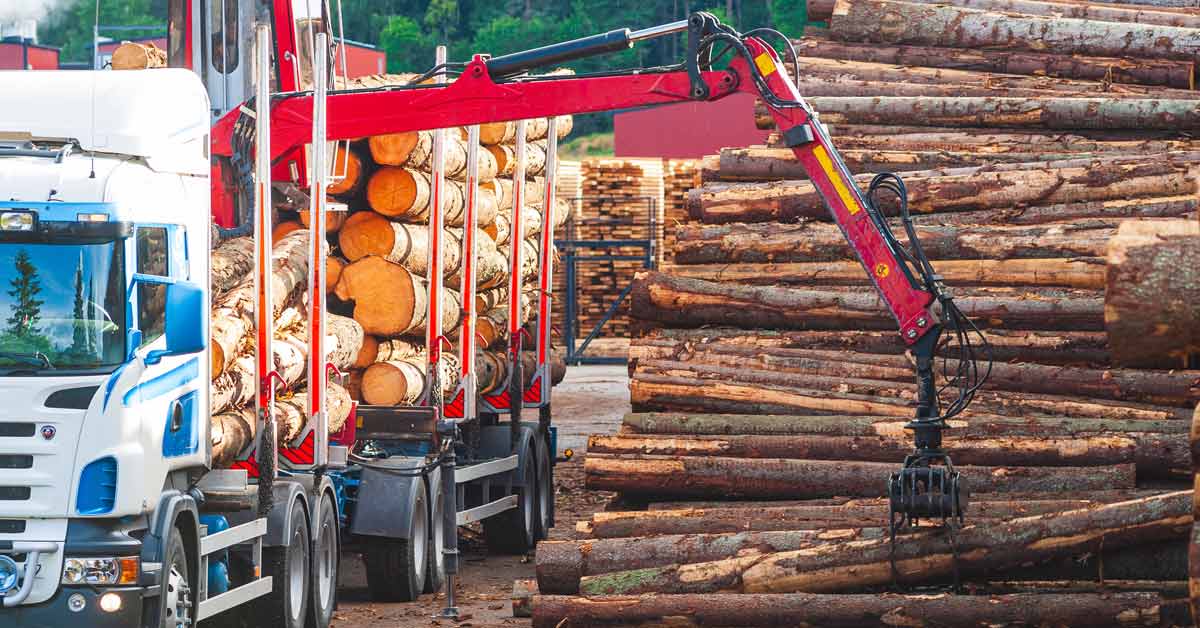
US–Canada Lumber Dispute Intensifies with Massive Tariff Increase
