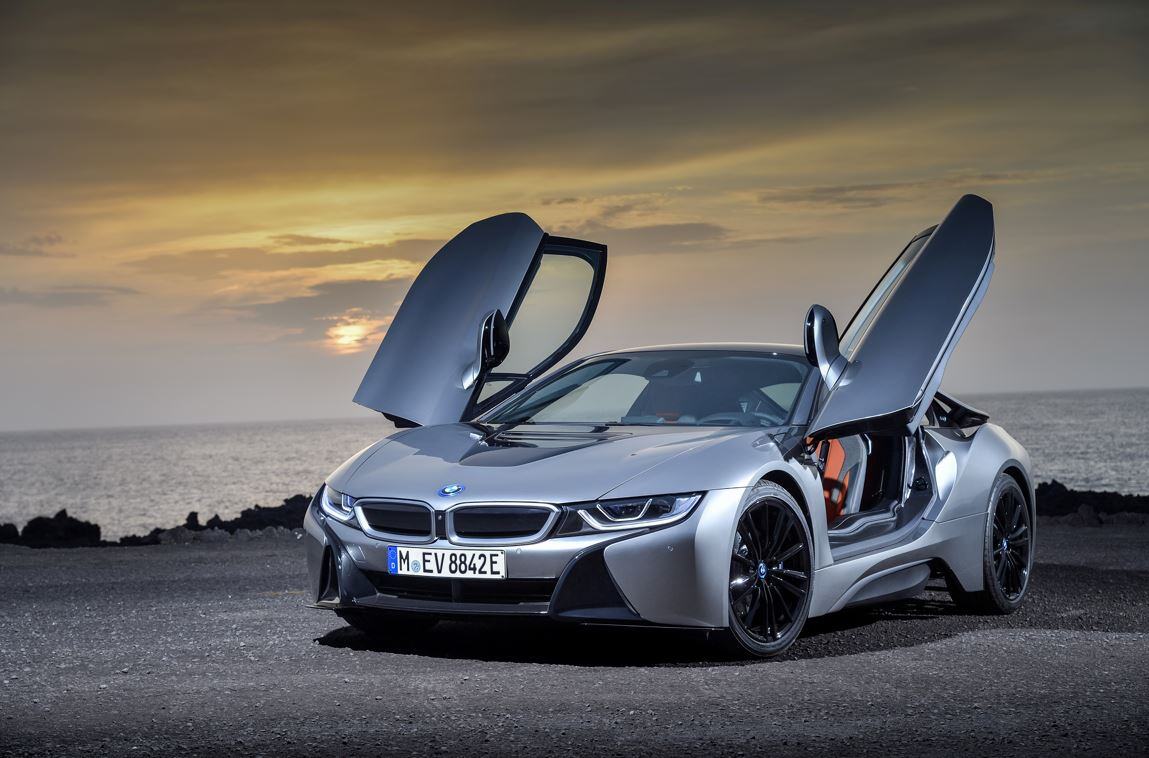
Encapsulating a building in popcorn may sound like a crazy way to boost energy efficiency... But researchers at Göttingen University’s Faculty of Forest Sciences and Forest Ecology in Germany have proven its suitability.
The material meets thermal insulation and fire-resistance parameters, and is water-repellent, the team says. Available commercially, the university’s quirky insulating material is part of a range that includes a popcorn-based binder for wood materials.
However novel they become; composites are not new. Egyptians used mud and straw mixtures in construction many thousands of years ago. However, as the methods and tools to analyze the structure–property and processing relationships of molecules evolve, so too do the materials under investigation.
Whether corn kernel-based composites will prove economically viable under real-world economic dynamics remains to be seen. But, for several reasons, composite manufacturing is gaining traction.
Composites are multiphase materials formed using a combination of different compounds bonded together. Blended, the materials provide properties unattainable from one component alone.
They comprise fibers and/or particles/flakes embedded in a matrix or layers of materials – or any combination thereof.
The Weight-Saving Race to the Minimum
Light-weighting is a key driver for composite materials innovation. Compared with average car weights of almost 1860 kg, the 1500 kg BMW i8 Coupé is exceptionally lightweight. Built up from an aluminum chassis, the vehicle’s passenger compartment is made of a high-strength carbon-fiber reinforced composite (CFRP).
Boeing revolutionized its 787-jet airliner range with a composite fuselage and wings. The 787 model is reportedly 80% composite by component volume and 50% composite by weight overall. And carbon fiber makes up 65% of the weight of each airplane’s 35 tons of CFRP.
Long before BMW and Boeing began innovating to reduce weight, the composite material sheet moulding compound (SMC) was commercialised. Developed for exterior car body parts, the material comprised both glass and carbon fibres. Since using SMC instead of steel reduced weight by 60%, and by 30% when replacing aluminum parts, it offered a way for the automotive industry to reduce the CO2 emissions of vehicle usage.
Polymer Matrix Composites
The most widely known composites comprise a synergic combination of high-performance fibers and a polymer matrix. In this blend, the fiber provides high strength, and the polymer spreads the load to provide resistance to weathering and corrosion. Thermosetting polymers allow for the formation of the reinforced article with optimum distribution of strength and stress resistance.
Maximum strength reinforced composite materials are achieved with a base of a mat of glass fibers, typically 5–10 mm thick. After lining or covering a model shape with the mat, it is sprayed with a liquid polymer, to which the catalyst has just been added, so that it begins to polymerize. A low-viscosity liquid polymer helps penetration of fiber mats. This method of fabrication is possible at room temperature. The curing phase (which involves the cross-linking of molecules) can alternatively be initiated by heat at around 150ºC rather than a catalyst.
The three best-known thermosetting resins used in composites are unsaturated polyester resins (UPR), vinyl esters, and epoxy resins. They find use in a range of applications including wind turbine blades, microwave cooker components as well as automotives and medical equipment.
The charts below demonstrate the diverse end uses for UPR in China and Europe. A large percentage of China's UPR usage goes to infrastructure. In Europe, however, this category is missing, probably due to a difference in classification. UPR use in transport is much greater in European countries than in China.
Source: Cefic European UP/VE Resin Association / Chinese Society for Composite Materials
Breakthrough in Thermoplastic Composites
Extending the scope of traditional fiber-reinforced thermosetting compounds is a relatively new matrix polymer, namely long fiber-reinforced thermoplastic (LFRT). Easily processed using standard molding equipment, LFRTs can deliver much higher mechanical performance than traditional short-fiber compounds.
LFRTs are available as pellets for use in injection molding and compression molding techniques. This not only brings enhanced mechanical properties and weight reduction to the molded article, but it also permits molding at speed. The two minutes molding cycle times sought by automobile manufacturers are possible with thermoplastics.
Thermosets, however, are not able to so readily meet such molding speeds. And, unlike thermosets, thermoplastic parts can be combined by heat, sonic, or induction welding. Adhesives and fasteners needed in thermosetting applications are eliminated with thermoplastic composites.
Common Thermoplastic and Fiber Composites
As the above table shows, fine glass fibers are commonly used in composite thermoplastics made with PET, polybutylene terephthalate (PBT), polylactide (PLA) and high-density polyethylene (HDPE), among others.
Acrylonitrile butadiene styrene (ABS) and polycarbonate-based composites are also commonly reinforced with glass – or steel – fibers. Glass fibers are also used in thermoplastic polyurethane (TPU) and polypropylene (PP) composites, and these plastics-based composite structures utilize carbon fiber reinforcement for the highest performance.
Composites made using polyamides – PA 6 or PA 66 – may feature carbon, steel, or glass fiber. Polyamide-based composites, however, are particularly suitable for a continuous filament-reinforced thermoplastic solution.
Continuous filament-reinforced thermoplastic composites are as strong as metal but offer the design freedom of plastics.
Charles Fryer, Senior Advisor, Tecnon OrbiChem
Unidirectional Tapes
Continuous filament-reinforced thermoplastics (CFRT) come in the form of unidirectional tapes. Filament is also used for woven sheets, filament winding, and pultrusion. These techniques permit more complex designs than with thermosets or metals.
Speaking on the sidelines of the JEC World Trade Show in Paris in 2019, independent consultant Michel Jansen highlighted engineered thermoplastics’ recent growth trajectory. He said, "Thermoplastics applications could be counted [sic] on the fingers of one hand in the early 2000s. In the years following, you could see thermoplastics composites growing."
Thermoplastic unidirectional tapes allow for stronger, lighter, smoother, and therefore better and, "Totally non-crimp - or near-zero crimp - products," Jansen said. "That's very beneficial for performance, while smoother surfaces mean better aesthetics."
"Every step in the supply chain from unidirectional tape to end product is mass scalable, so you can really scale it up to mass production which is crucial for the industry," he added.
Out of this World
Aromatic polyamide fiber – also known as Aramid – is ideal for PA 6 and 66 composite applications. A high-performance fiber, its molecules comprise relatively rigid polymer chains. Aramid is a high-strength material with good resistance to abrasion and organic solvents – qualities that also make it suitable for aerospace and military applications.
Polyetheretherketone (PEEK) and polyetherimide (PEI) composites are preferred for use in the aerospace and aviation industry. PEI has high heat and radiation resistance. It has been used in aerospace antennae equipment as well as for Airbus and jet plane floor paneling. PEEK's mechanical performance and thermal resistance set it apart, as well as its chemical and hydrolysis resistance.
With the performance capabilities of materials in constant a state of flux as the boundaries of molecular science, the future of composites is strong. Today popcorn keeping you warmer, tomorrow... Who knows? The only limit is in the imagination.
Tecnon OrbiChem's business information platform OrbiChem360 covers most of the plastics for composite structures.
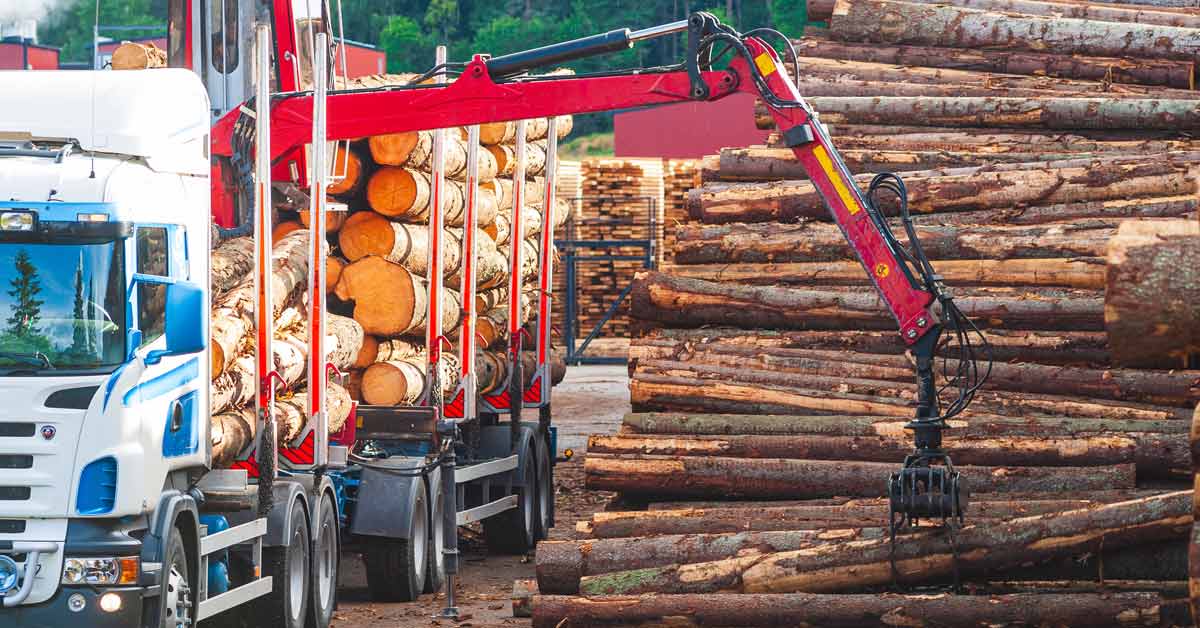
US–Canada Lumber Dispute Intensifies with Massive Tariff Increase
